Plan and prepare for a production
This sub process describes the requirements, recommendations and guidelines STAND has, which may be relevant in planning and preparation for a production of a product to be sold in the retail trade.
In addition to the finished product, raw materials and other input factors included in the finished product are also included, as well as packaging, load carriers / pallets used for transportation and storage of the finished product.
The areas described are:
- Shelf life requirements and possible use of dynamic shelf life
- Requirements for pallets planned for palletization of manufactured products
- Requirements for the packaging as planned to be used on manufactured products
- Traceability requirements for raw materials and input factors planned to be used in production
Allocation of total shelf life on a product
Reducing food waste is an overall goal in society. Food waste related to exceeding the limit values of shelf life between the parties in the value chain, constitutes a significant part.
Surveys shows that food waste are significantly reduced if the store and the consumer have a larger part of the total shelf life.
It is therefore a goal that the producer and distributor consume the least amount of available time and that the maximum amount of time is exposed to the consumer.
The grocery industry has defined one Table for allocation of shelf life of a product which regulates the responsibility for and expectations the recipient of products has, linked to shelf life. Online players with b2c sales will be defined as retailers when dividing total shelf life.
In case of minor exceedances of the table’s limit values, participants are expected to seek solutions that provide the lowest possible food waste.
The parties are encouraged to develop performance and collaborate to reduce consumption of shelf life.
Endringslogg
Determine total shelf life of a product and requirements for labelling this
The responsibility for determining type of shelf life labelling and total shelf life lies with the manufacturer. The shelf life is calculated from the time the product is ready for sales, for example from after the product has been matured and checked.
The actual shelf life of the product is affected by a variety of conditions, primarily the properties of the raw material and the external impact.
The manufacturers are encouraged to assess whether dynamic shelf life labelling can be practiced.
This means that total shelf life can be expanded when conditions allows for this to be done.
The number of days marked on a product may therefore be more than the number of shelf life on selected products.
According to the Mattilsynet (Norwegian Food Safety Authority), the use of dynamic shelf life is within the current regulations.
Labelling
The packaging (Consumer Units (CU) and Stock Keeping Units (SKU)) shall be labelled according to the manufacturer’s choice of type of shelf life and total shelf life.
Evaluate the use of dynamic shelf life
“Expiry date overdue” is the main reason for food waste in the value chain. A more flexible shelf life labelling throughout the year could help reduce food waste.
Shelf life is affected by several conditions that may vary. It is possible to specify increased shelf life in periods of time or for batches. This is termed as “dynamic shelf life». In practice, it means that overall shelf life can be expanded when conditions give the opportunity to do so.
The supplier should inform the customer if dynamic shelf life is applied.
According to the Mattilsynet (Norwegian Food Safety Authority), the use of dynamic shelf life within the current regulations: “It is the manufacturer who assesses and puts the shelf life of the food products. Manufacturers know the raw materials and processes used. Shelf life should be based on common and realistic conditions for transportation, storage and sales. This does not prevent manufacturers from taking into account that there may also be different external conditions for the shelf life of the foodstuffs. In practice, manufacturers often put the shelf life out of the most demanding but realistic conditions throughout the year. If the business has full control and overview of the terms, nothing stops them from choosing different shelf life throughout the year for the same product. This means the food is given a shelf life that is adapted to season, temperature and other conditions.”
More information can be found here: http://www.mattilsynet.no/mat_og_vann/merking_av_mat/generelle_krav_til_merking_av_mat/holdbarhetsmerking_paa_matvarer.2711
Examples of using dynamic shelf life that could have longer shelf life than often is the practice today:
- Different temperatures throughout the year
In order to make a realistic assessment, the producer assumes that the products are stored in normal outdoor / room temperature for a shorter period of time through the value chain, such as transshipment, stock refills in stores, consumer carts, transport from store to home and in the home (in and out of the fridge and on the kitchen table). In summer, the outdoor / room temperature is higher and thus has a greater impact on shelf life. To make a realistic assessment, it’s normal to take into account the assumptions in the summer period and determine the shelf life based on this, and the same shelf life is normally used throughout the year.
- Different shelf life based on different technology
Different companies may have different production methods and / or hygiene standards. To make a realistic assessment, the starting point is the technology that provides the shortest shelf life.
- Different shelf life of raw materials
The regulations or internal rules stipulate that raw materials that are up to x days “old” may be used at any given time in the manufacturing process. Then the shelf life is determined by using x-day-old raw material each time. This even though you often use fresher raw materials than x days.
- Different raw material quality
Raw material quality may vary naturally over a year, and in some cases this may affect shelf life. To make a realistic assessment, the raw material with the shortest shelf life is used, and normally uses the same shelf life of the finished foods throughout the year.
Dynamic shelf life and the EPD database
There is no need for any changes to the EPD database to utilize dynamic shelf life.
It is the product’s shortest shelf life during the year the supplier must register in the EPD database.
Valid pallets
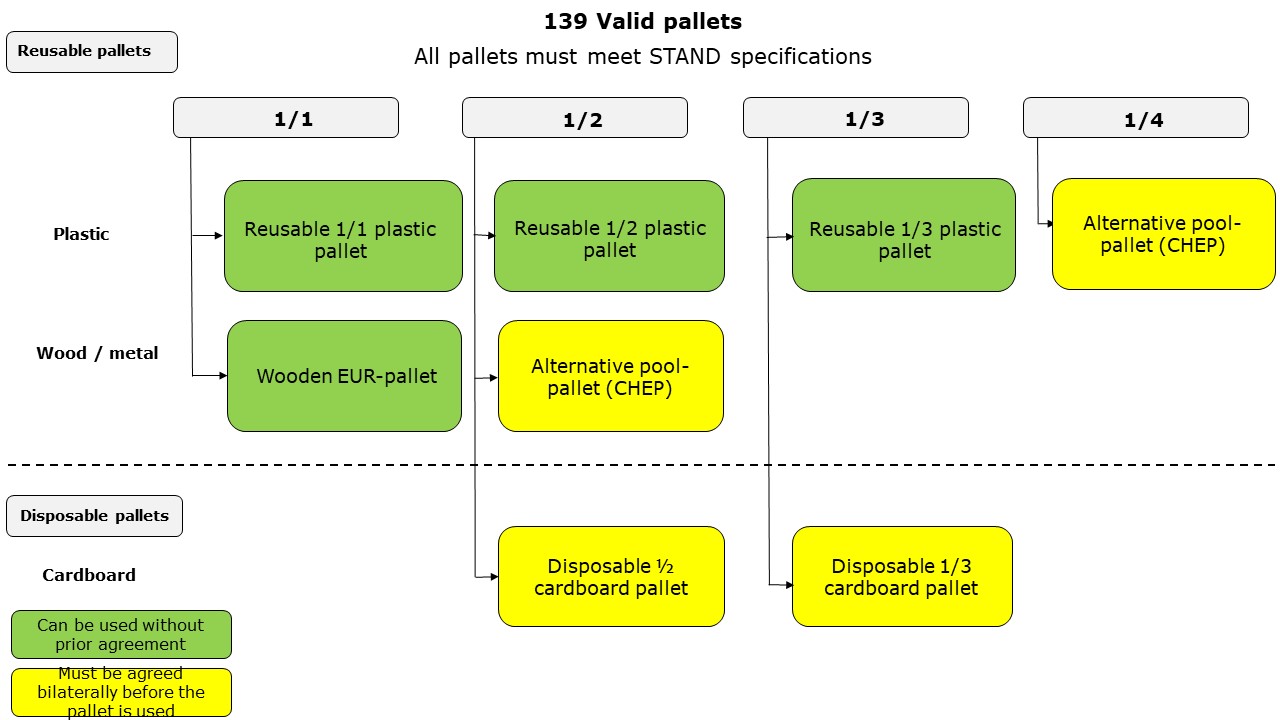
This is an animation that show what pallets are valid for distribution.
Requirements specifications can be downloaded here:
Requirements for approved EUR-pallets
Specification for reusable 1/1 plastic pallet
Specification for reusable 1/2 plastic pallet
Requirements specification for reusable 1/3 plastic pallet (from NLP)
Specification for reusable 1/4 plastic pallet
Requirements Specification reusable 1/2 wooden pallet
Requirements specification for 1/3 and 1/2 disposable cardboard pallet
Requirements for design of Stock Keeping Unit (SKU) and packaging
Stock Keeping Unit (SKU) is the unit the retailer buys.
Stock Keeping Unit (SKU) occurs in various forms, such as carton, reusable box / pallet box, intermediate carton and such.
The most important task of the Stock Keeping Unit (SKU) is to secure Consumer Units (CU) from the time of manufacturing until it is finished exposed in a shop shelf.
The number of Consumer Units (CU) in a Stock Keeping Unit (SKU) is determined by the manufacturer, preferably in dialogue with the distributor / retail chain.
The Stock Keeping Unit (SKU) must be adapted to the modular system, see Modular system
for picking and grouping of products can be done as efficient as possible.
Case fill rate shall be calculated. This is described in Case fill rate
Stock Keeping Unit (SKU) must be designed to withstand the strain required in the value chain.
Automatic warehouses require that Stock Keeping Units (SKU) must be packed in a way that it can be lifted, stacked, clamped and handled with different mechanized devices, see Automated warehouse at distributor – greater understanding of the depalletization process.
Design requirements and packaging
When designing a Stock Keeping Unit (SKU), it must be based on the modular system.
This means that the Stock Keeping Unit (SKU) should not be less than 100 x 150 mm and not more than 400 x 600 mm.
Example of best practices
Modular Stock Keeping Unit (SKU).
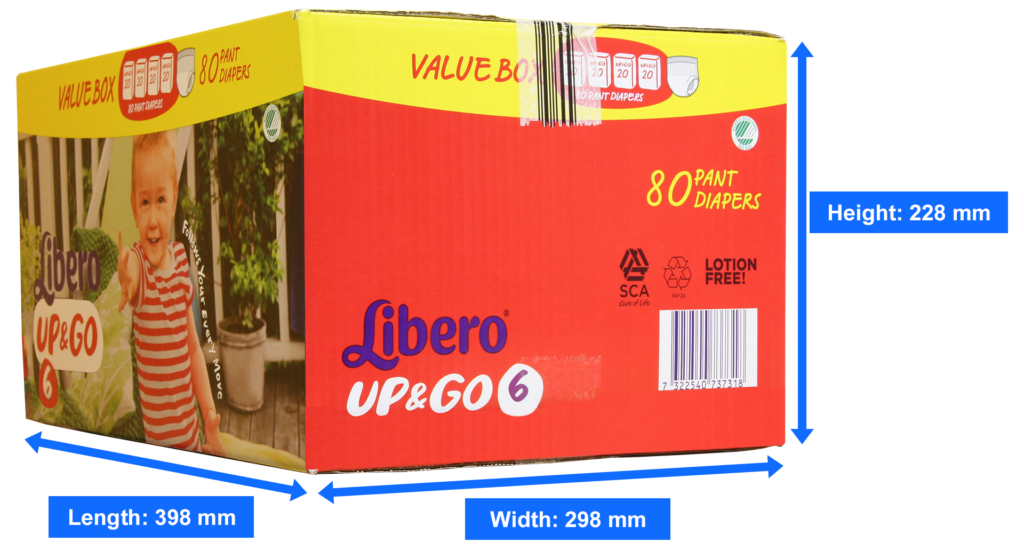
Example of an inappropriate Stock Keeping Unit (SKU)
Stock Keeping Unit (SKU) is not adapted to the modular system.
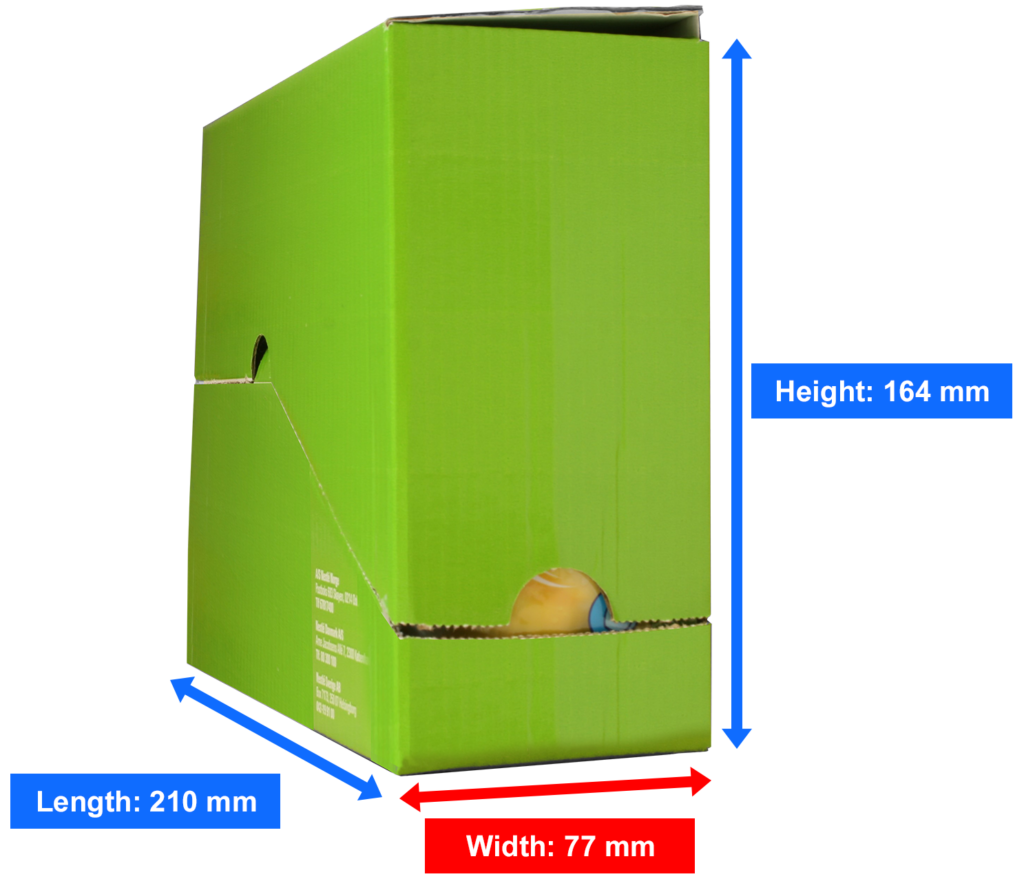
The size of the Stock Keeping Unit (SKU) must consider the size of the shelf space for the current product group.
The short side of the Stock Keeping Unit (SKU) should be front where appropriate.
There must be a simple and clear opening guide, preferably with illustration.
The packaging must be opened without using a knife.
When the Consumer Units (CU) is exposed in the Stock Keeping Unit (SKU), the least possible of the Stock Keeping Unit’s (SKU) packaging should be visible when exposed in the store shelf.
Stock Keeping Unit (SKU) must not weigh more than 15 kg.
Stock Keeping Unit (SKU) must be in recyclable cardboard or plastic.
Example of an inappropriate Stock Keeping Unit (SKU)
Lid / plastic film is missing, which may cause Consumer Unit (CU) to fall out during internal transport.
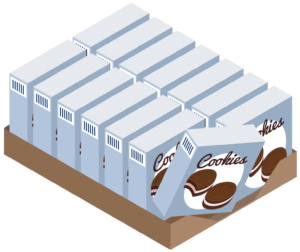
Plastic boxes – all variants – must be considered to work in automated warehouse handling.
Stock Keeping Unit (SKU) must be form stable.
Example of best practices
Stock Keeping Unit (SKU) is form stable.
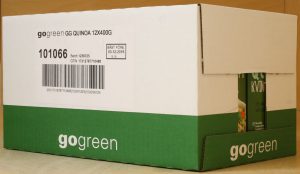
Example of best practices
Form stable Stock Keeping Units (SKU) that embraces close to its content and is strong enough to not deform.
Resists load on inbound transport (2 pallets in height), as well as handling through the value chain.
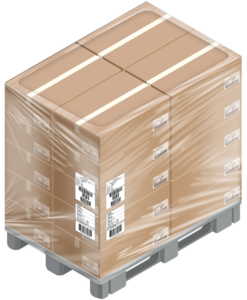
Example of an inappropriate Stock Keeping Unit (SKU)
Not form stable. Do not resist strain on inbound transport (2 pallets in height), as well as handling through the value chain.
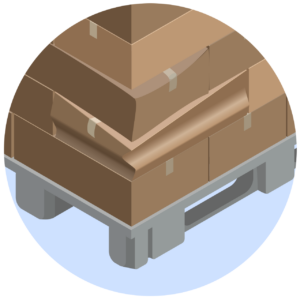
Stock Keeping Unit (SKU) that is only wrapped in plastic foil must have a tray / trough below.
Example of best practices
Stock Keeping Unit (SKU) on tray / trough with plastic wrap.
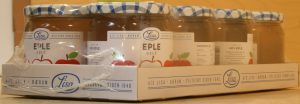
Stock Keeping Units (SKU) must have straight sides.
Example of best practices
Stock Keeping Units (SKU) with straight sides.
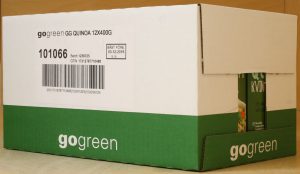
Glue quality and amount of glue on Stock Keeping Unit (SKU) must be such that glued surfaces do not loosen.
Example of best practices
Glue quality and amount of glue is such that glued surfaces do not loosen.
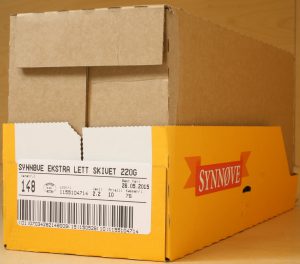
Constructed example of an inappropriate Stock Keeping Unit (SKU)
Too little glue / too few glue points are included that flap gaps with subsequent stops in automatic warehouse systems.
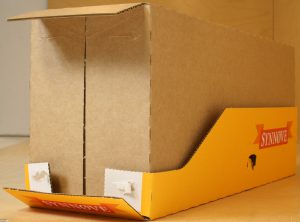
The Stock Keeping Unit (SKU) should be stackable and “ears” should only be used where it is necessary for stability.
Should “ears” be used, these should not exceed 5mm and should not be used in conjunction with intermediate pallet sheets.
Stock Keeping Unit (SKU) should not have loose lid.
The lid must be attached to the tray / trough in such a way that it does not loosen during handling. It is recommended to use glue points or a locking mechanism.
The Stock Keeping Unit (SKU) must have a center of gravity relative to the base that allows it to be handled on conveyor belts.
The height / width ratio should be below 1.7 to ensure that the products do not fall under internal transport in an automatic warehouse.
Example of best practices
The ratio height / width is below 1.7.
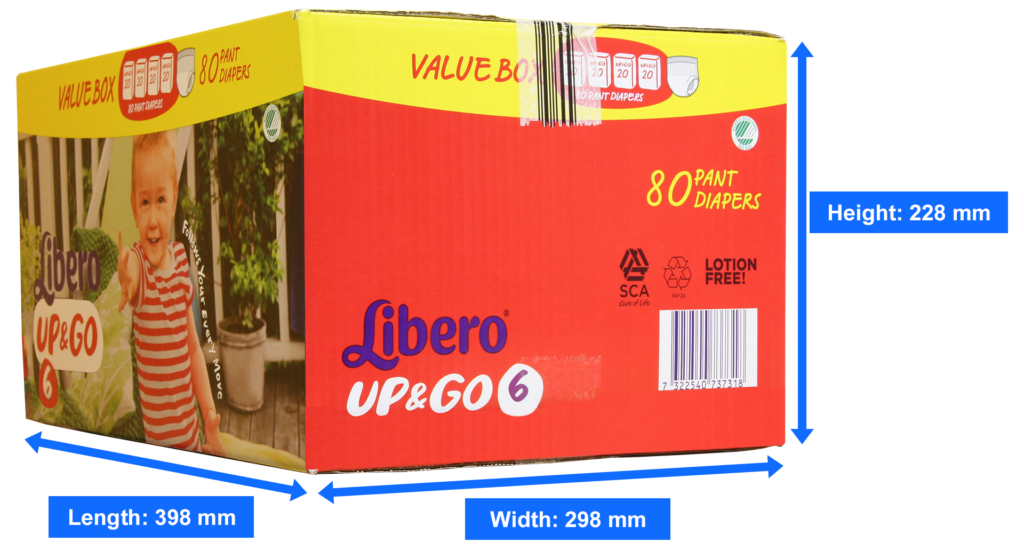
Example of an inappropriate Stock Keeping Unit (SKU)
The height / width ratio is over 1.7, which means that the Stock Keeping Unit (SKU) can fall during internal transport.
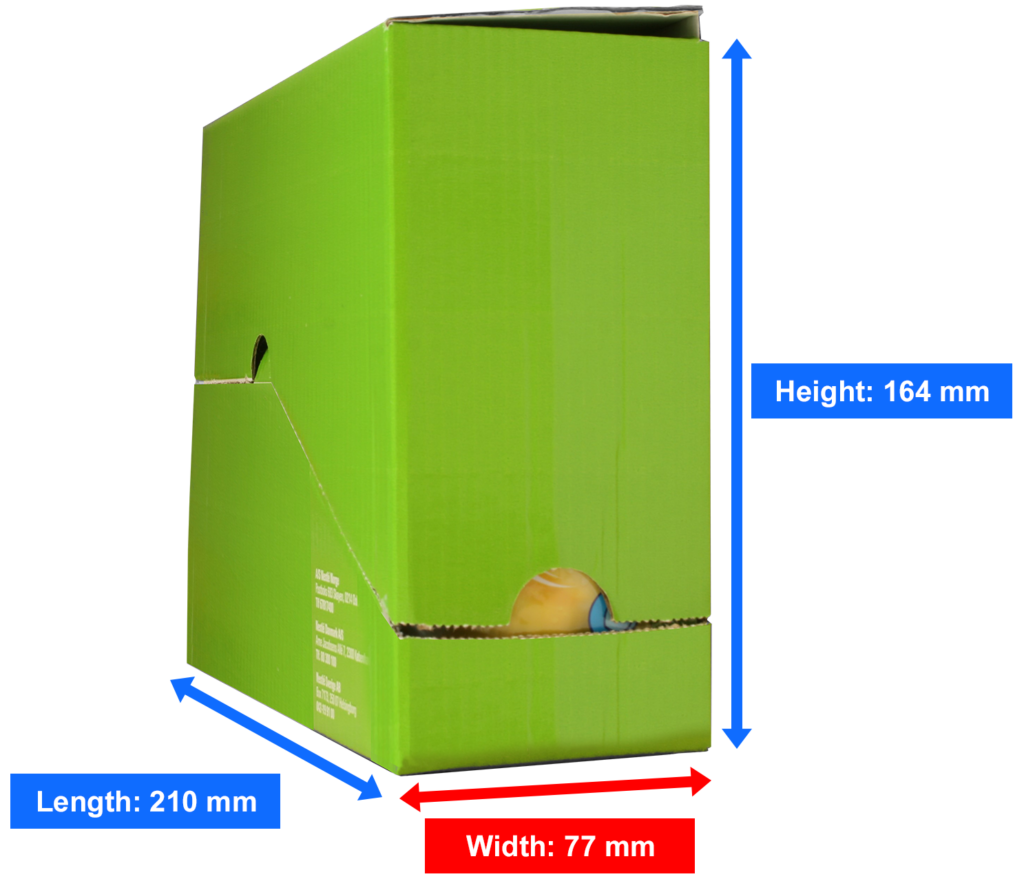
Stock Keeping Unit (SKU) exposure front should not be less than 30 mm, regardless of the chosen solution.
The information on the Consumer Unit (CU) must be visible.
Packaging capacity
During the design of the product and packaging it must be considered that the outer dimensions of the finished Stock Keeping Unit (SKU), tray and otherwise, under the load of the above-mentioned product packaging, due to bulging, is within the margin. In practice, this can be from 0.5 to 1.0 cm.
Optimal transport requires the use of load capacity of the transport systems (weight and height).
Generally, the packaging should be able to carry a similar pallet (2 identical pallets) without any breakage or clamping damage during transport and storage.
Exceptions from this must be specified and labelled on the (Distribution Unit (DU).
Method of calculation of carrying capacity is described in Top load labelling system.
The packaging shall be able to withstand shipping with other products for shipping to the store in a rational way.
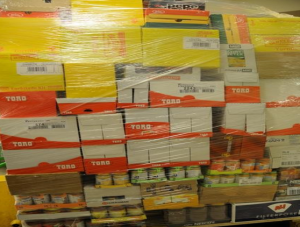
In order to achieve the industry’s common goal of efficient flow of products, reduced negative environmental impact, promoted sales and reduced losses, it is important to focus on:
- Top load
- Stackability
- Module customization
Especially for reusable boxes / pallet boxes
Basically, Stock Keeping Units (SKU) is desired in cardboard, or in combination with plastic.
Reusable boxes are an alternative to Stock Keeping Units (SKU) in corrugated paper but must be agreed bilaterally.
Particularly for Intermediate cartons
The use of Intermediate cartons should be kept as low as possible and must be agreed bilaterally.
Intermediate cartons are accepted in cases where the Stock Keeping Unit (SKU) solution is not possible because the Stock Keeping Unit (SKU) does not meet the requirements for strength, stability or size and where the use of intermediate pallet sheet on pallet is not possible.
The intermediate carton must be labelled so that it clearly differs from the Stock Keeping Unit (SKU) and shall not weigh more than 15 kg.
Guidelines and routines for tracking, recall and withdrawal
In its framework, STAND has defined guidelines, recommendations and best practices for how products should be marketed in the distribution chain, and how information on this should be exchanged between the parties.
Central to this is the consideration of the consumer and his expectation for safe food.
The guidelines for tracking, recall and withdrawal do not define food quality requirements, but describe what procedures and processes the industry has established to mitigate any unwanted effects should an incident or crisis occur in a product.
Best practices
The guidelines describe best practices in this area.
By following STAND’s framework, the guidelines will be achievable for all parties involved.
Some important prerequisites for best practice.
- Routines and processes must be simple, predictable and intuitive
- Products and deliveries / load carriers must be labeled in a unified, standardized and correct way so that they can be traced through the value chain.
- Product information must be registered in the Tradesolution EPD
- Detailed tracking information must be exchanged digitally between the parties and follow the products through the value chain.
- Action must be taken quickly when an incident or crisis occurs
By ensuring that a total industry complies with STAND’s framework, consumers’ demands and expectations for safe food are fully met.
Objective of the guidelines
The guidelines are aimed at “Contribute to meet consumers’ expectations for safe products”.
Target Audience:
- Anyone who may or will be involved in any recall or withdrawal
- Everyone involved in the production or labeling of products and packaging covered by the guidelines
Products / areas to which the guidelines apply:
- Recommended for food and non-food products, except pharmaceuticals
- Other inputs, plants, animals or foodstuffs
- Materials and articles that are intended to come into contact with, or may affect, inputs or foodstuffs.
Medicines are exempt from the guidelines. Here we refer to separate regulations, not described here.
Certain types of food may be subject to additional regulatory requirements beyond what is described here. An example is the EU’s new tobacco directive (EU 2014/40) which make the requirements for traceability of tobacco products more stringent, but is not described here.
Product tracking requirements
The legislation requires that each company must have systems to document which products are purchased from each supplier and which customer has purchased the company’s finished products.
This also includes raw materials and other input that are covered by the legislation.
There is no requirement in the legislation for which type of systems to be used for this.
Businesses can practice more comprehensive tracking systems than the minimum regulatory requirements require, but this is either based on self-imposed requirements or agreements with, and orders from the contracting parties.
Tracking means being able to follow the physical flow of goods. This is often referred to as chain traceability, and assumes that all parties meet the requirements and follow the guidelines for tracking.
Tracking takes into account the legal requirements for all parties to be able to trace their products one step forward and one step back in the value chain.
Tracking one step forward:
This means to the address the products are delivered to.
An invoice system containing information about item number / item name, customer number / customer name and invoice date is sufficient to be able to trace one step forward in the value chain.
If the company is using batch/lot numbers for their products, this should be included in the invoice, despatch advice and the like, or linked directly to the company’s own systems.
Tracking one step backward:
This means the address from which the products are delivered.
The company must keep a log of received products describing which products were purchased from whom and in which quantitiy, and date.
If the addresses for where products are delivered from or delivered to are not in accordance with the legal ownership of the products and the invoice process, this should be agreed separately between the parties.
Requirements for tracking information and labeling
The main purpose of the tracking information is to lay the groundwork for effective blocking, withdrawal or recall of products.
Central tracking information is:
- GTIN (Global Trade Item Number) – Unique identification of products
- GLN (Global Location Number) – Unique identification of trading parties, pick-up points, delivery points etc.
- SSCC (Serial Shipping Container Code) – Unique identification of load carriers / pallets
- Batch / lot number – A unique batch or lot number defined by supplier / manufacturer
- Shelf life – Either Best Before date or Last Consumption Date
It is a requirement that the products are labeled to enable tracking.
The marking must be affixed to the product packaging and legible.
The following applies to finished goods traded between supplier and distributor / retailer:
Information to be marked:
- The name of the supplier
- Product name/description
- Product number identified with a GTIN.
- Best before date / last day of consumption date, if required
- Batch / Lot number, if required
Load carrier (for example pallet) shall be marked with SSCC.
The sender must in his system have an overview of which recipient the product was sent to, and also the recipient must have an overview of which sender the product was received from. Both sender and recipient must be identified with GLN.
Sender shall in his system register:
- Quantity sent
- Shipping Date
- Reception date (if known)
Recipient shall in his system register:
- Quantity received
- Shipping date (if known)
- Reception Date
The following applies to raw materials and other inputs:
- GTIN should be used for identification of inputs / raw material, if available
- GLN should be used for identification of sender / suppliers, if available
More about tracking information and how the product can be tracked in the value chain is described here Recommended traceability methods in the value chain.