The top load labelling system
Recommendation for industry and retailers
The system ensures that there is a minimum of product damage and to enable automated and efficient load planning throughout the industry.
It is recommended to the industry to work with its suppliers with the aim of maximizing the quantity of products satisfying the recommendation and that all products are labelled with permission top load.
Part A
Cost-effective transport requires optimal utilization of the factors capacity, weight and volume. The ratio between the average weight of the products and the volume is essentially such that trucks can be fully utilized. However, the reality is that due to different heights on the pallets it is not possible to load trucks and containers in such a way that the volume is utilized. This implies significant and unnecessary additional costs in the supply chain.
Developing a common system to determine the load a pallet can withstand based on the optimal use of packaging consumption will result that the entire industry can achieve better transport utilization and thereby a significant cost reduction, also in a national economic perspective, and contribute to positive environmental impact.
Prerequisites
The system is based on the following assumptions:
- Secondary packaging shall protect primary packaging and the product during storage, handling and transportation until the product is made available to the consumer at the store
- The packaging must withstand the dynamic load by placing two pallets of products on top of each other in real transport conditions.
- The industry is responsible for developing proper packaging for its products through a conscious commitment to total economic optimization. Safety factor determined by the product manufacturer
Labelling
When using the top load labelling system, STAND recommends that a pallet should be able to withstand its own weight by labelling the pallets with an additional information with maximum top load.
With permissible top load is understood, the weight of the pallet which can be placed on top of a specified pallet should withstand. The pallet should withstand the top load weight without the packaging or the products in the packaging on the underlying pallet being damaged during normal handling and transport.
Note that there is a specific weight to be specified and not a weight class. The use of single weights provides the greatest flexibility and thus the ability to optimize the utilization of the carrier’s loading capacity.
Allowed top load to be labelled is as follows:
- As part of the standard pallet label (GS1 pallet or product label with its own section)
- On transport label (GS1 transport label with separate section)
- On your own label (exception when it is not practical with a) or b).
Transport label with top load information:
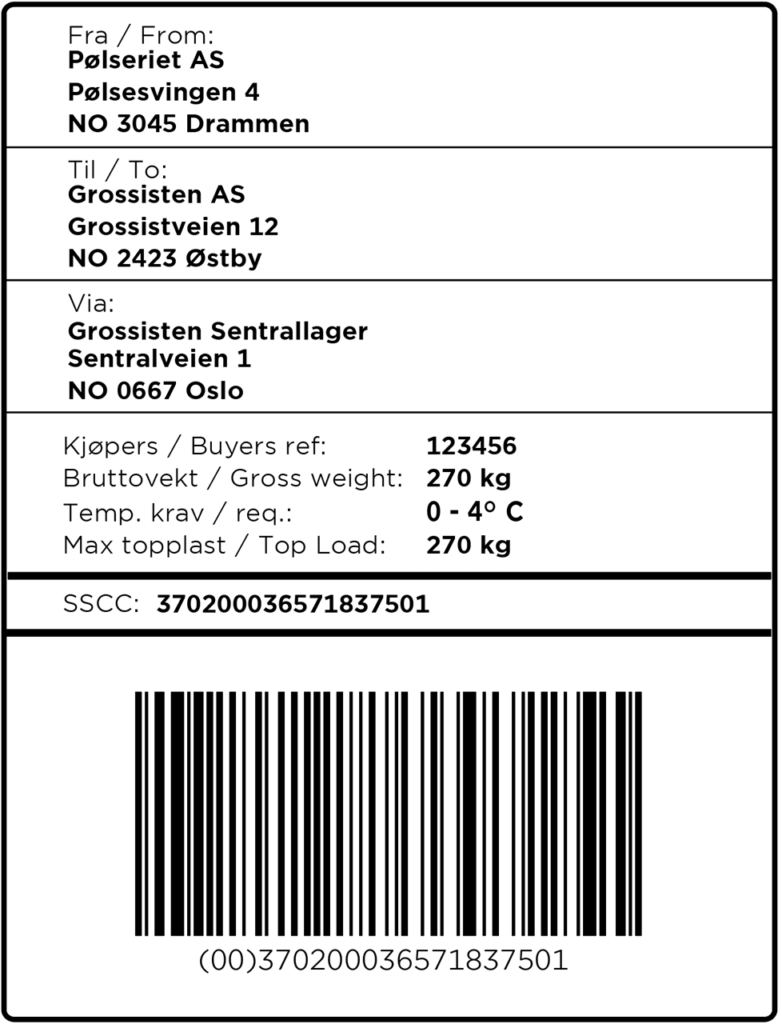
Pallet label with top load information:
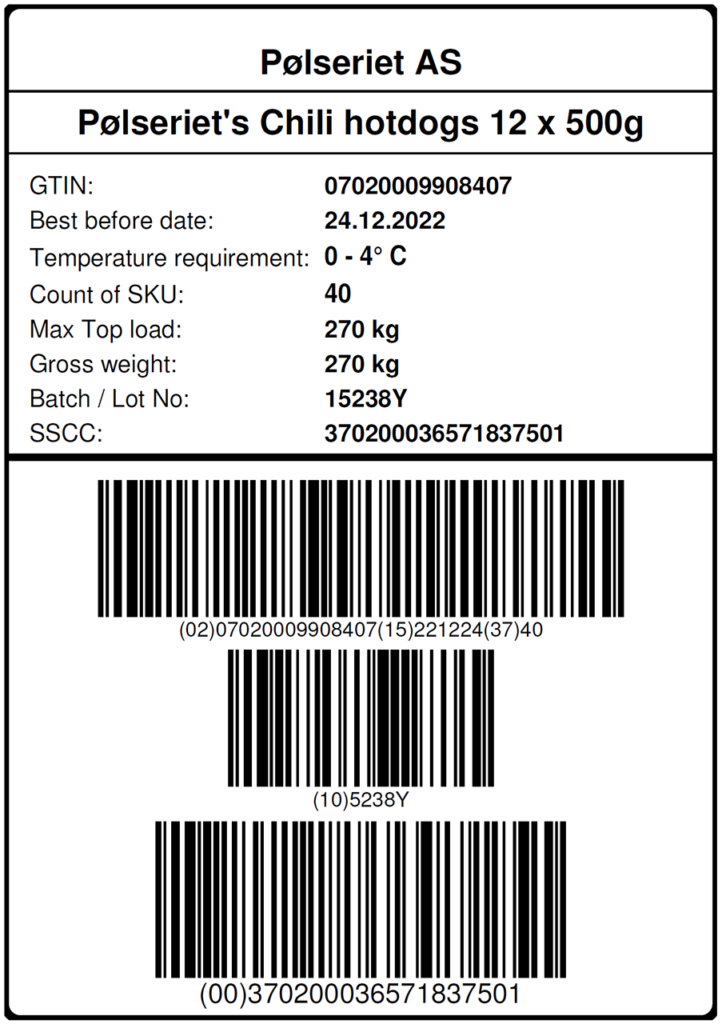
PART B
Packaging design
It is recommended that it is how the finished Distribution Unit (DU) / pallet should look like, is the starting point. Then create the design and development of Stock Keeping Units (SKU) and Consumer Units (CU) on this. Close collaboration with space management is required for the optimal design of the products in the store shelves.
Strength calculation
It is assumed that the Stock Keeping Unit (SKU) strength calculation is normally performed to withstand pressure loads, see PART C.
Practical testing may be the only way to determine the packaging’s ability to withstand pressure loads.
Compression test
For all packaging except for a single corrugated cardboard box where calculation may be sufficient, it is assumed that a compression test of Stock Keeping Units (SKU) and Stock Keeping Units (SKU) filled with Consumer Units (CU), regardless of whether Consumer Units (CU) will provide a portion of the load capacity, is assumed.
Norwegian cardboard suppliers have developed their own calculation and test procedures for corrugated cardboard.
For other packaging, manufacturers’ standards, possibly an independent test institute, are used, see PART C.
Safety factor
To reach the maximum permitted top load for a packaging unit and for a pallet of units, consideration must be given to all matters relating to design, materials and applications.
This happens in practice by reducing calculated values by a percentage reduction for different conditions that weaken the packaging.
In addition, a safety factor depends on transport conditions that will compensate for any unforeseen impacts such as the packaging and the pallet may be exposed on its way.
See PART C for more detailed information.
Transportation test
It is recommended that the system in each company contain requirements for transport testing as standard.
In all cases, where there is a new or normative package and for all cases where the consequences of breakage may be particularly large, a transportation test is performed to ensure that the product behaves as provided, even under unfavorable conditions.
A transportation test must therefore be carried out in an environment which will cause the packaging to be subjected to at least the impacts that normal transportation will have.
This is the responsibility of the industry / supplier.
Cost
- Upgrading the efforts around packaging development
- IT system for load scheduling with efficient use of top load information
- Upgrade of labelling equipment
Savings
- Reduced shipping costs
- Reduced breakage
- Reduced return transport
- Fewer errors and corrections during development of packaging
- Correct placement of the products in warehouse
PART C
Strength calculation (Example)

Safety factor
There are several factors that affect the choice of safety factor for transport. These can be divided into the following main groups;
- the packaging itself
- how the packaging is stacked on the pallet (pallet pattern)
- the location of the packaging on the pallet (overhang/underhang)
- environmental impacts from temperature
The correct safety factor is the responsibility of the product manufacturer.
The security factor must consider conditions that cannot be predicted and thus easily establish the calculations.
Therefore, with the use of a safety factor, it is necessary to assess whether the relevant requirement is within normal transport and handling or not. Determining the safety factor is a relationship between the packaging manufacturer and the product manufacturer, but it is the product manufacturer who is responsible for ensuring that there is no breakage during transport to the consumer.
Sample of security factor
The factor may be set to SF = 3.5. This means that if the packaging is specified to withstand a pressure load of 350kg, it will be approved and marked for 100kg load
under the type of dynamic conditions that occur during normal transportation and handling in Norway.
The packaging
The starting point for the strength of the packaging is the choice of material and construction.
A weak material can be designed to give a high strength construction, and a strong material may be impaired by choice for wrong purposes (incompatible materials), improper processing (stress, fracture or cracking), poor knowledge, etc.
This applies to perforation, tape, pressure that compresses the wave (“flute”) on corrugated cardboard, affixing labels etc.
In addition, especially moisture will weaken the packaging and thereby the strength significantly.
Reduction of strength due to these conditions will normally be part of the work performed by the packaging supplier as part of the development work.
Pallet pattern
There are in principle two different ways to stack products on a pallet (pallet patterns); bond stacking pattern and column stacking pattern.
Bond stacking means that the units on each layer are different than the ones above and under, thus locking each other to a greater or lesser extent, but it reduces the compressive strength by approx. 40 %.
Column stacking means stacking packages on top of each other without overlapping with other packages. This form of stacking gives maximum strength in terms of pressure load due to that the corners are bigger breach stiffness than the sides, but the stack gives poor stability without additional use of stretch film, strap, ribbon or similar.
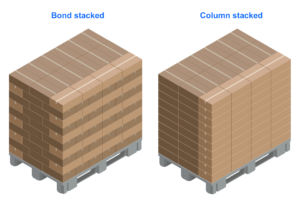