Development of a product
Suppliers are encouraged to work closely with packaging suppliers and customers in developing new products.
Suppliers are encouraged to work closely with suppliers of packaging and customers in the process of developing new products.
The grocery industry is heavily packaging intensive. Increasing demands and expectations from authorities and consumers for reduction in use of virgin fossil materials and replacing plastic, whenever possible, will be highly focused. “Design for recycling” will be crucial to meet future regulations, expectations, environmental requirements and recycling goals.
Reduction of food waste will have increased focus to meet reduction targets agreed by the trade and the Norwegian authorities.
The grocery value chain in Norway has for many years exercised responsibility by active ownership in the material return shemes for packaginxg Grønt Punkt Norge and by funding the company Matvett to prevent food waste. These organizations are available to support you introducing more sustainable products.
Areas affected by, and subject to guidelines from STAND are:
- Optimization and requirements for design of Consumer Unit (CU), Stock Keeping Unit (SKU) and Distribution Unit (DU) with accompanying packaging materials
- The modular system
- Case fill rate
- The top load labelling system
- Automatic warehouse at distributor – increased understanding of depalletization process
- Checklist
- Valid pallets and requirements for these
- Labelling requirements
- Guidelines for how to label Consumer Unit (CU) with 2D barcode
- Purpose of labelling of Stock Keeping Unit (SKU) and Distribution Unit (DU)
- Product information on Stock Keeping Unit (SKU), with example of Stock Keeping Unit (SKU) label
- Guidelines for labelling of Stock Keeping Units (SKU)
- Product information on Distribution Unit (DU), with example of Distribution Unit (DU) label
- Labelling of transport information
- Guidelines for labels on Distribution Units (DU)
- Bar code requirements for labelling with GS1-128 on Distribution Unit (DU)
- Shelf life
- Determine total shelf life of a product and labelling requirements
- Allocation of shelf life between the players in the value chain
- Use of dynamic shelf life
- Bilateral agreements for allocation of shelf life
- Traceability of a product
- Guidelines for traceability, recall and withdrawal
- Requirements for traceability of products and the product areas covered by this
- Requirements for traceability information and labelling
- Alternative ways to track and trace an item in the value chain
Endringslogg
Optimization of Consumer Unit (CU), Stock Keeping Unit (SKU), Distribution Unit (DU) and packaging – central to the development of new/changes to existing products
The grocery industry has a common goal of being able to:
- Streamline product flow
- Reduce environmental impact
- Promote sales
- Reduce shrinkage
when products are being developed/changed.
To achieve this, it is crucial to standardize and optimize packaging on the product at all packaging levels – Consumer Unit (CU), Stock Keeping Unit (SKU) and Distribution Unit (DU).
STAND has therefore prepared a standard for this, which applies to all packaging levels.
Audience for the standard is managers and everyone who works with product development, assortment and logistics in the value chain.
By complying with the standard, processes in the value chain are optimized and gains can be extracted in a number of areas such as:
Warehouse
- Form Stable Distribution Units (DU) and Stock Keeping Units (SKU)
- Correct quality of Distribution Units (DU) and Stock Keeping Units (SKU) for efficient handling through warehouse
Outbound transport
- Withstand double stacking
- Avoids shrinkage and damage
Inbound transport
- High case fill rate
- Double stacking of pallets
- Avoiding transport damage
Shop
- Effective replenishment
- Sales-friendly, good visibility when Stock Keeping Unit (SKU) is used to expose products
- Optimal use of shelf space
- Reduced food waste, with correct number of Consumer Units (CU) in Stock Keeping Unit (SKU)
- Reduced food waste, utilising 2D barcodes with dynamic information
Consumer
- Optimal and user-friendly packaging
- Clear, accurate and complementary product declaration
- Recycling labelling
- Extended product information utilising 2D barcodes
In addition, optimization of packaging through compliance with the standard will reduce environmental impact at all stages in the value chain, as part of the industry agreement with the authorities.
The packaging must be:
Easy to sort
In order for the packaging to be able to be recycled, it is important that it is sorted correctly by the end user and thus enters the correct recycling stream. There are a number of steps you can take when designing the packaging, which increase the likelihood that it will be sorted correctly. This information is summarized at https://www.grontpunkt.no/design-for-kildesortering
Recyclable
In order for the packaging to be material-recycled and become new raw material that can be used to make new products, it is important that this is taken into account in the packaging design and material selection. To find out how recyclable the packaging is and what steps can be taken to improve this, you can enter the packaging in https://kalkulator.grontpunkt.no
In monomaterial if possible
The easiest way to make it more intuitive for the end user to sort the packaging correctly, and to make it easier to recycle the packaging, is to ensure that the packaging only consists of one material.
From recycled material if possible
Most packaging is recycled, but there is too little demand for recycled material. By using recycled material when developing new packaging, you ensure that the circular material flows work and thus both reduce the need for virgin raw material and the environmental burdens these entail.
Important notice
All products must follow the GS1 Allocation rules. (chapter 2.4). These are international rules and are mainly based on the fact that a change of over 20% to a physical dimension, on any axis, or gross weight, requires assignment of a new GTIN.
In addition, the following applies to Norway:
- For products registered in the Tradesolution EPD base, approval of the grocery chains is required to keep existing GTIN on a product, also for changes below 20%
- Frequent cumulative changes, without changing the GTIN, in avoidance of the 20% rule is an unacceptable practice. Trading partners should be notified about all dimensional changes. Cumulative changes might cause problems for trading partners and may obstruct the transport and supply of a product
- Local, national or regional regulations may require more frequent GTIN changes. Such regulations have precedence over the rules provided within the GTIN Management Standard
Exception from the standard
Under special conditions, exceptions from industry standards and guidelines may be relevant.
Exceptions must be agreed separately between the parties concerned and shall be described in Checklist for optimization of Consumer Unit (CU), Stock Keeping Unit (SKU) and Distribution Unit (DU).
The check list can be downloaded as a separate document.
Requirements for design of Consumer Unit (CU)
Consumer Unit (CU) is the unit the consumer purchases in store.
Consumer Unit (CU) must be designed to optimize use of shop shelves and other furnishings. In addition, the information on the Consumer Unit (CU) should be visible even when the package is on a tray on the shelf.
Consumer Unit (CU) should be easy to open and to use.
Consumer Unit (CU) should be, included Stock Keeping Unit (SKU) and Distribution Unit (DU) adapted to the modular system, see Modular system
Unnecessary volume not containing the product itself in the packaging should be limited to what is necessary to protect the product. If necessary, secure against shrinkage (small, valuable Consumer Units (CU)).
Quantity (packing content) in Consumer Unit (CU) is determined by manufacturer, preferably in dialogue with distributor / retail chain.
Case fill rate shall be calculated. This is described in Case fill rate
On new products, it is expected that the case fill rate is higher than the average of the product group to which it belongs.
Measurement of the case fill rate related to the product launch windows was carried out by DMF until 2018. When switching to a new product classification system, historical data could not be compared, as the timeline and product groupings from 2014 were changed.
Efforts to increase the case fill rate in the grocery industry are important from both an environmental and efficiency perspective.
In collaboration with the industry, Tradesolution has developed some new reports for measuring the case fill rate in the grocery industry. Suppliers and retailer chains that have access to the EPD base can see the case fill rate for the products they have access to directly in the database. Here you can see the actual case fill rate on basic product (BASIS-level) and calculated case fill rate for the packaging levels above.
Log in her and feel free to contact the EPD base helpdesk at epd@tradesolution.no if you have further questions.
Guideline for labelling 2D barcodes on Consumer Units
Background
The need for information both in trade and to the consumer is constantly increasing. Today’s solution using the EAN-13 barcode does not provide opportunities for additional machine-readable information. The need for more information has led to products that have more than one bar code applied to Consumer Units, which creates challenges both at the checkout point (POS) and in the value chain. Often this is a QR code with a link to a website where the consumer can find more information.
In parallel with the need for more communication with consumers, a need is emerging at the retail level to gain more control over the traceability and expiry date of the products, to ensure safe food and reduce food waste. This is happening in most countries in the world. In Norway, GS1 Norway, together with Matvett, established a working group consisting of representatives from brand suppliers, grocery chains, system suppliers and other stakeholders to discuss these issues. These guidelines are a result of this work and have now been included as part of STAND’s framework for the Norwegian grocery industry.
Purpose of the use of 2D barcodes in Norwegian grocery
Although 2D barcodes are not the only solution to the challenges, this is the data carrier of the future, where the need for information is greater than just identifying a product with GTIN. 2D barcodes take up less space, can contain more information about the product, are a tool for reducing food waste and increase food security, are more flexible, and can be read by mobile phones. This provides an opportunity for increased consumer contact. In addition, 2D barcodes can solve all needs for information exchange throughout the supply chain, including being able to link to websites.
Different types of 2D barcodes
There are many different 2D barcodes, but only some of them can be used in connection with the GS1 standards, which are the standards used by the Norwegian grocery industry. The different 2D barcodes are also used for different purposes. This is regulated in GS1’s regulations, General Specifications. The difference between the different 2D barcodes helps to determine what they can be used for.
QR Code
The QR Code barcode is in the GS1 system defined to be used only with GS1 Digital Link URI syntax. In practice, this means that this should only be used for communication with the consumer via a URL that links to a website with more information that the consumer can read with his mobile phone. QR Code has grown to become the preferred barcode for consumer communication and most mobile phones today are able to read this with the built-in camera app in the phone. This means that the threshold for reading QR Code is low among consumers, and it is less need for training and communication to put functionality related to QR Code into production. Here you can find more information about QR codes.

GS1 Datamatrix
GS1 Datamatrix is a variant of Datamatrix that uses GS1 Element String syntax. This is the use of AI (Application Identifier) structure. This is a way of structuring the information in the barcode so that everyone who reads the barcode understands the content in the same way regardless of the order in which the information is printed and how much information is in the barcode. According to GS1 General Specifications, GS1 Datamatrix is only permitted for use on Consumer units with variable measure and prescription medicines. However, it is permitted to use it in limited pilots, for test purposes and in closed value chains under controlled conditions. The advantage of GS1 Datamatrix is that it has high compression and error correction. It can be printed both square and rectangular so that it can fit where there is not enough height, but enough width to get the information needed without compromising on size and thus readability. However, the rectangular version has a limit on the amount of data that can be used. GS1 Datamatrix is the only permitted barcode on prescription drugs. Here you can find more information about GS1 Datamatrix.
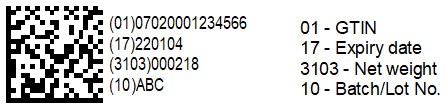
Content in barcode
A minimum requirement for information attributes has been defined for POS purposes.
This is:
- GTIN
- Best before date or Expiry date
- Batch/lot nr.
- Weight (for variable measure products).
It is possible to use other Application Identifiers for internal and/or external needs, but this is then up to each individual actor to use.
Requirements for design of Stock Keeping Unit (SKU) and packaging
Stock Keeping Unit (SKU) is the unit the retailer buys.
Stock Keeping Unit (SKU) occurs in various forms, such as carton, reusable box / pallet box, intermediate carton and such.
The most important task of the Stock Keeping Unit (SKU) is to secure Consumer Units (CU) from the time of manufacturing until it is finished exposed in a shop shelf.
The number of Consumer Units (CU) in a Stock Keeping Unit (SKU) is determined by the manufacturer, preferably in dialogue with the distributor / retail chain.
The Stock Keeping Unit (SKU) must be adapted to the modular system, see Modular system
for picking and grouping of products can be done as efficient as possible.
Case fill rate shall be calculated. This is described in Case fill rate
Stock Keeping Unit (SKU) must be designed to withstand the strain required in the value chain.
Automatic warehouses require that Stock Keeping Units (SKU) must be packed in a way that it can be lifted, stacked, clamped and handled with different mechanized devices, see Automated warehouse at distributor – greater understanding of the depalletization process.
Design requirements and packaging
When designing a Stock Keeping Unit (SKU), it must be based on the modular system.
This means that the Stock Keeping Unit (SKU) should not be less than 100 x 150 mm and not more than 400 x 600 mm.
Example of best practices
Modular Stock Keeping Unit (SKU).
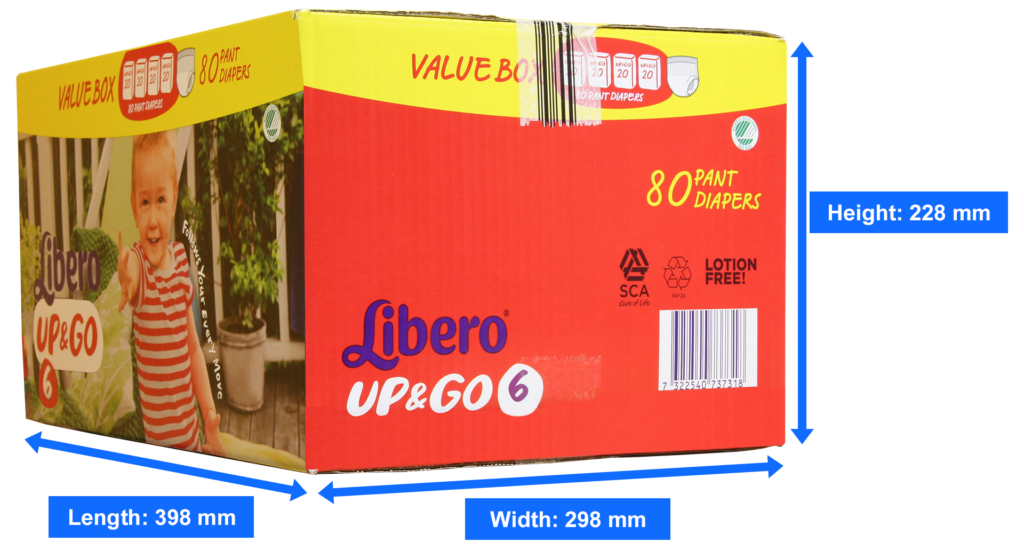
Example of an inappropriate Stock Keeping Unit (SKU)
Stock Keeping Unit (SKU) is not adapted to the modular system.
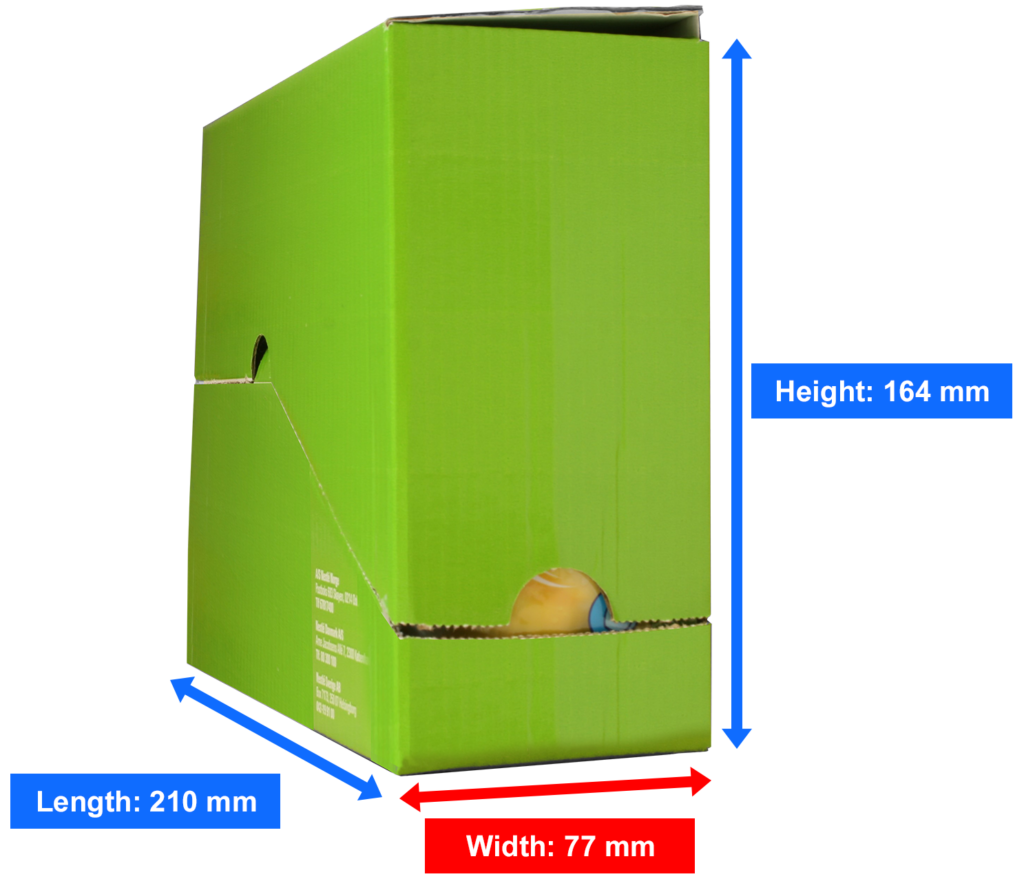
The size of the Stock Keeping Unit (SKU) must consider the size of the shelf space for the current product group.
The short side of the Stock Keeping Unit (SKU) should be front where appropriate.
There must be a simple and clear opening guide, preferably with illustration.
The packaging must be opened without using a knife.
When the Consumer Units (CU) is exposed in the Stock Keeping Unit (SKU), the least possible of the Stock Keeping Unit’s (SKU) packaging should be visible when exposed in the store shelf.
Stock Keeping Unit (SKU) must not weigh more than 15 kg.
Stock Keeping Unit (SKU) must be in recyclable cardboard or plastic.
Example of an inappropriate Stock Keeping Unit (SKU)
Lid / plastic film is missing, which may cause Consumer Unit (CU) to fall out during internal transport.
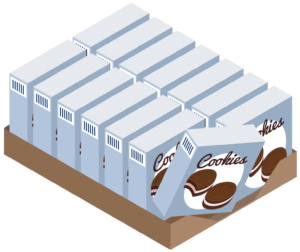
Plastic boxes – all variants – must be considered to work in automated warehouse handling.
Stock Keeping Unit (SKU) must be form stable.
Example of best practices
Stock Keeping Unit (SKU) is form stable.
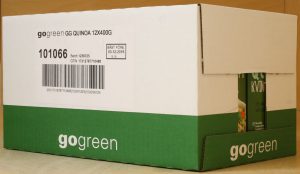
Example of best practices
Form stable Stock Keeping Units (SKU) that embraces close to its content and is strong enough to not deform.
Resists load on inbound transport (2 pallets in height), as well as handling through the value chain.
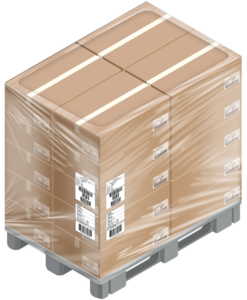
Example of an inappropriate Stock Keeping Unit (SKU)
Not form stable. Do not resist strain on inbound transport (2 pallets in height), as well as handling through the value chain.
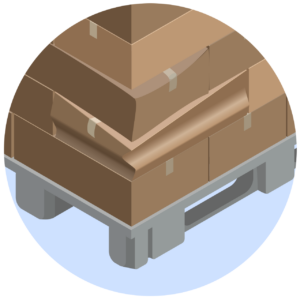
Stock Keeping Unit (SKU) that is only wrapped in plastic foil must have a tray / trough below.
Example of best practices
Stock Keeping Unit (SKU) on tray / trough with plastic wrap.
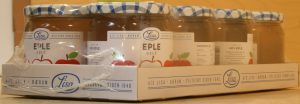
Stock Keeping Units (SKU) must have straight sides.
Example of best practices
Stock Keeping Units (SKU) with straight sides.
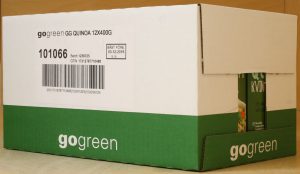
Glue quality and amount of glue on Stock Keeping Unit (SKU) must be such that glued surfaces do not loosen.
Example of best practices
Glue quality and amount of glue is such that glued surfaces do not loosen.
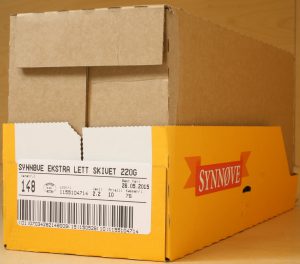
Constructed example of an inappropriate Stock Keeping Unit (SKU)
Too little glue / too few glue points are included that flap gaps with subsequent stops in automatic warehouse systems.
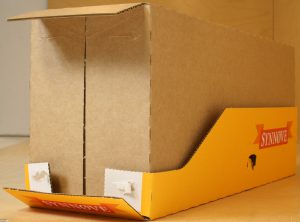
The Stock Keeping Unit (SKU) should be stackable and “ears” should only be used where it is necessary for stability.
Should “ears” be used, these should not exceed 5mm and should not be used in conjunction with intermediate pallet sheets.
Stock Keeping Unit (SKU) should not have loose lid.
The lid must be attached to the tray / trough in such a way that it does not loosen during handling. It is recommended to use glue points or a locking mechanism.
The Stock Keeping Unit (SKU) must have a center of gravity relative to the base that allows it to be handled on conveyor belts.
The height / width ratio should be below 1.7 to ensure that the products do not fall under internal transport in an automatic warehouse.
Example of best practices
The ratio height / width is below 1.7.
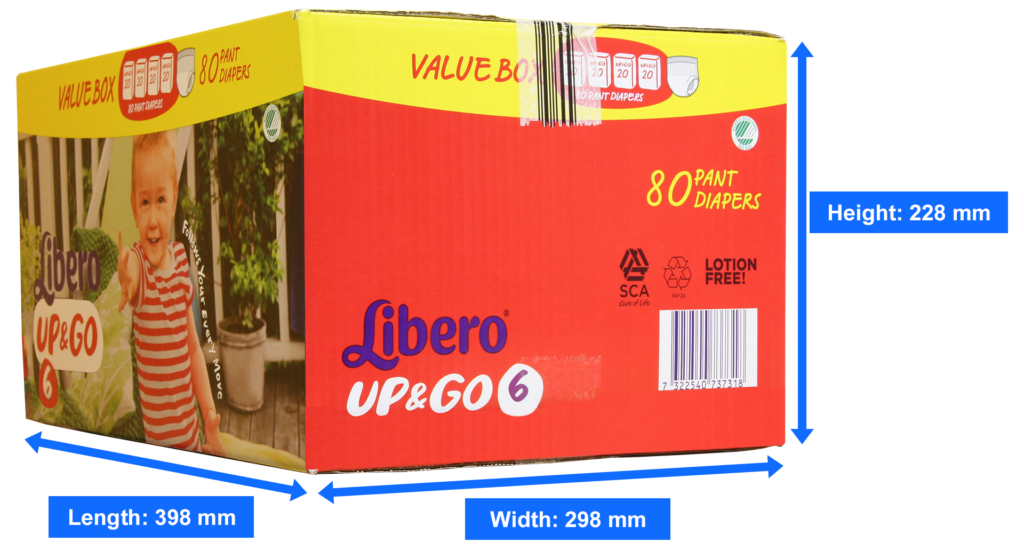
Example of an inappropriate Stock Keeping Unit (SKU)
The height / width ratio is over 1.7, which means that the Stock Keeping Unit (SKU) can fall during internal transport.
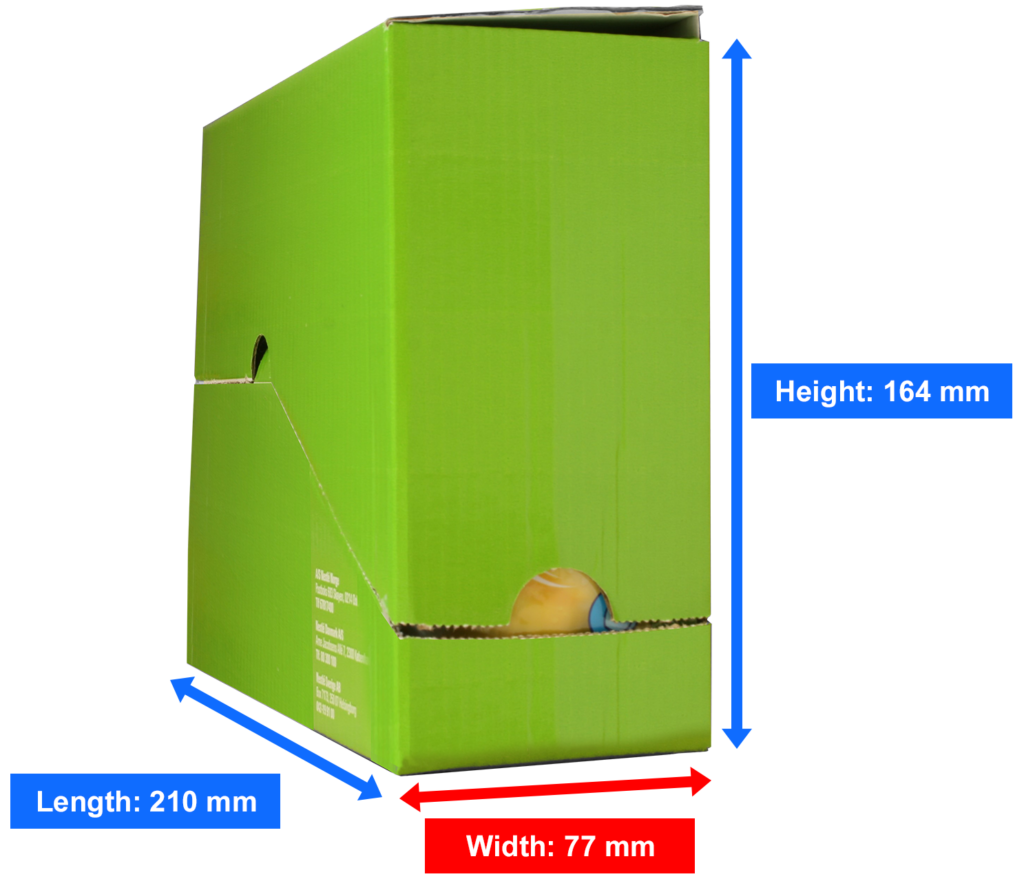
Stock Keeping Unit (SKU) exposure front should not be less than 30 mm, regardless of the chosen solution.
The information on the Consumer Unit (CU) must be visible.
Packaging capacity
During the design of the product and packaging it must be considered that the outer dimensions of the finished Stock Keeping Unit (SKU), tray and otherwise, under the load of the above-mentioned product packaging, due to bulging, is within the margin. In practice, this can be from 0.5 to 1.0 cm.
Optimal transport requires the use of load capacity of the transport systems (weight and height).
Generally, the packaging should be able to carry a similar pallet (2 identical pallets) without any breakage or clamping damage during transport and storage.
Exceptions from this must be specified and labelled on the (Distribution Unit (DU).
Method of calculation of carrying capacity is described in Top load labelling system.
The packaging shall be able to withstand shipping with other products for shipping to the store in a rational way.
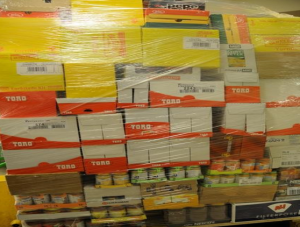
In order to achieve the industry’s common goal of efficient flow of products, reduced negative environmental impact, promoted sales and reduced losses, it is important to focus on:
- Top load
- Stackability
- Module customization
Especially for reusable boxes / pallet boxes
Basically, Stock Keeping Units (SKU) is desired in cardboard, or in combination with plastic.
Reusable boxes are an alternative to Stock Keeping Units (SKU) in corrugated paper but must be agreed bilaterally.
Particularly for Intermediate cartons
The use of Intermediate cartons should be kept as low as possible and must be agreed bilaterally.
Intermediate cartons are accepted in cases where the Stock Keeping Unit (SKU) solution is not possible because the Stock Keeping Unit (SKU) does not meet the requirements for strength, stability or size and where the use of intermediate pallet sheet on pallet is not possible.
The intermediate carton must be labelled so that it clearly differs from the Stock Keeping Unit (SKU) and shall not weigh more than 15 kg.
Requirements for the design of the Distribution Unit (DU) and palletization
The Distribution Unit (DU) is the unit the Stock Keeping Units (SKU) is stacked on / packed in for transport to distributor.
Design of a Standard pallet (Standard pallet and Standard pallet – Low)
A Standard pallet must contain the same product (same GTIN) with a fixed number of Stock Keeping Units (SKU), in a fixed pallet pattern, with equal number of Stock Keeping Units (SKU)on each layer, and where labelling of unique product information on the Distribution Unit (DU) is possible.
The pallet structure shall contain as little excess volume of “air” as possible.
Standard pallet
Maximum pallet height must be 1200 mm incl. pallet. All pallets with total height above standard 1200mm with maximum height of 1250 mm to be agreed bilaterally between supplier and their customers.
Tolerance limit for existing products is 1249 mm.
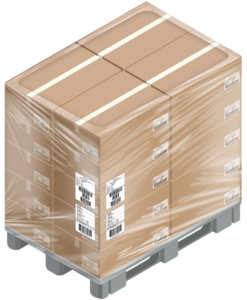
Standard pallet – Low
Maximum pallet height shall be 600 mm incl. pallet.
Standard pallet – Low is used for low-frequency products and for products with short shelf life.
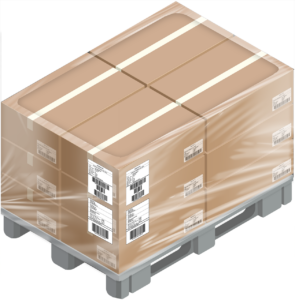
Principles for the construction of a palletpattern, central in calculation of top load weight, ref Top load labelling system.
When creating a pallet pattern, the following applies:
- A packaged Distribution Unit (DU) must be form stable and handling-friendly
- A Distribution Unit (DU) shall withstand regular transport, handling and storage through the value chain
- For single article Distribution Units (DU), all layers must contain the same number of Stock Keeping Units (SKU), and in a fixed pallet pattern
- Requirements for equal number of Stock Keeping Units (SKU) on each pallet / identical layer from pallet to pallet, with the possibility of variation between the layers
- The pallet should not have overhang
- The Stock Keeping Unit (SKU) should be placed on the pallet as it is exposed in the store
- Do not glue between pallet layers or between Stock Keeping Units (SKU) in the same pallet layer
- If a transport label or product label is attached directly to Stock Keeping Unit (SKU), the label must not overlap between 2 Stock Keeping Units (SKUs), either horizontally or vertically
- All pallets with total height above standard 1200mm with maximum height of 1250 mm to be agreed bilaterally between supplier and their customers.
Types of pallet pattern
When constructing Distribution Units (DU), the Stock Keeping Unit (SKU) must be placed in accordance with a given pallet pattern. These are referred to as bond stacking and column stacking. Pallets can also be built as a combination of bond stacking and column stacking.
Bond Stacking
Bond Stacking means that the units on every other layer are different, thus locking each other to a greater or lesser extent, but it reduces the compressive strength by approx. 40%.
Example of good pallet utilization and stacking with bond stacking, for good stability.
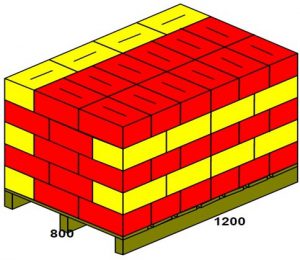
Column Stacking
Column stacking means stacking packages on top of each other without overlapping with other packages. This form of stacking gives maximum strength in terms of pressure load due to that the corners have better roll stiffness than the sides, but the stack gives poor stability without additional use of shrink wrap, strap, ribbon or similar.
Example of column stacking in the lower pallet layers, and bond stacking on the top layer. Combining the different stacking methods achieves good stack strength on the lower layers while the pallet is locked on top.
This is often a good alternative to intermediate pallet sheets.
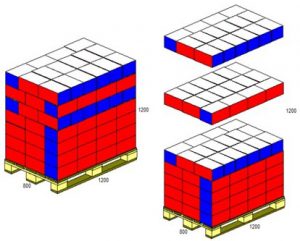
Use of plastic to secure the pallet through the value chain
- Shrink / stretch film must not be so tight that the packages are deformed
- Shrink / stretch film must be tight around to the pallet
- No tail of plastic must hang loose
- Shrink / stretch film must not cover the fork lift openings on the pallet
- Shrink / stretch film must not be fastened around the pallet blocks
Use of intermediate pallet sheets
Intermediate pallet sheets must be minimized and used only if this is necessary to ensure quality and transportability of the pallet.
Intermediate pallet sheets are preferred if the alternative to this is intermediate cartons, “Ears” on the Stock Keeping Unit (SKU) or use of corner trims.
Where intermediate pallet sheets are used, the following requirements apply:
- The pallet sheet to be used for standard euro pallet should have dimensions of 750 mm * 1150 mm, ie 50 mm less than the length and width of the current load carrier
- The pallet sheet must be of rigid cardboard or corrugated cardboard.
- The stiffness of the pallet sheet must pass the following test: If the short edge of the plate hangs 500 mm from a flat surface (eg a table), the pallet sheet must not bend down more than 50 mm, see illustration below
- No more than one intermediate pallet sheet between each layer
- The intermediate pallet sheet must not be fastened and be flat
- Only a whole intermediate pallet sheet, i.e. without holes or perforations, shall be used
- In case of questions, one is encouraged to contact the packaging supplier
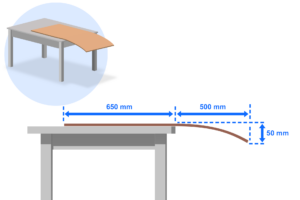
See also Automated storage at distributor – greater understanding of the depalletization process
Example of intermediate pallet sheet that does not meet quality requirements. The intermediate pallet sheet is a thin paper and is not suitable for automatic warehouse systems
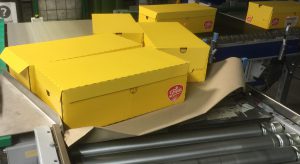
Example of what happens when using “thin paper” intermediate pallet sheets.
The sheet is hanging down in the robot. It blocks for sensors that check that the layer is separated from the rest of the pallet. The robot will stop, and manual error correction must be carried out before the machine can be restarted.
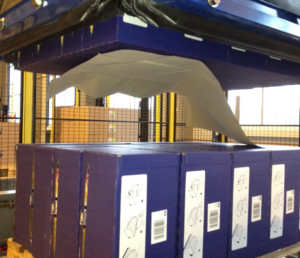
Example of pallet with intermediate pallet sheets, too big – hanging on outside the pallet.
Is not suitable.
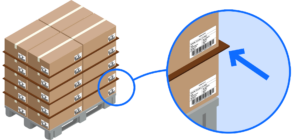
Intermediate pallet sheets with holes. Is not suitable.
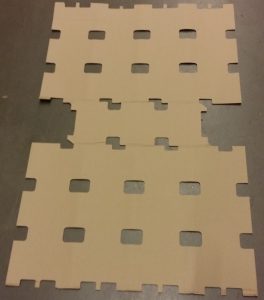
Endringslogg
Placement of Stock Keeping Unit (SKU) on pallet
It is a prerequisite for maintaining strength, that Stock Keeping Units (SKU) are placed within the edges of the pallet with a small margin.
Devices placed on or outside the edge can cause damage with subsequent reduced carrying capacity / risk of injury.
The pallet area should be utilized as best as possible with products. By following the Modular system optimal use of the pallet is ensured and reduces the risk of the load shifting during transport.
Overhang is not accepted.
Valid pallets
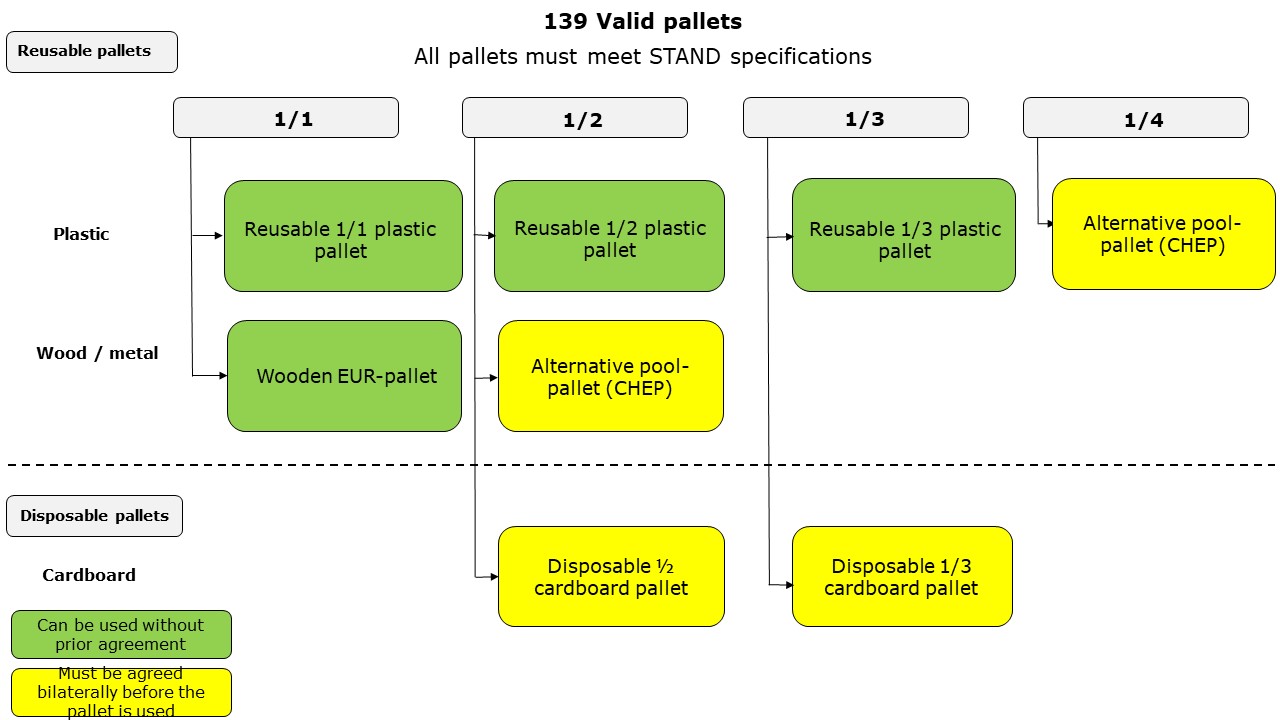
This is an animation that show what pallets are valid for distribution.
Requirements specifications can be downloaded here:
Requirements for approved EUR-pallets
Specification for reusable 1/1 plastic pallet
Specification for reusable 1/2 plastic pallet
Requirements specification for reusable 1/3 plastic pallet (from NLP)
Specification for reusable 1/4 plastic pallet
Requirements Specification reusable 1/2 wooden pallet
Requirements specification for 1/3 and 1/2 disposable cardboard pallet
Purpose of labelling of Stock Keeping Unit (SKU) and Distribution Unit (DU)
The purpose of a standard for labelling of Stock Keeping Unit (SKU) and Distribution Unit (DU) with subsequent electronic data interchange (EDI) is to:
- Achieve an efficient flow of products from manufacturer to consumer
- Ensure traceability through the value chain, which is important in case an event or crisis occurs which requires a recall or withdrawal of the product
The basis for this is the labelling of each Distribution Unit (DU) with a unique SSCC.
This code is the main key in the electronic Despatch Advice and is linked to information about which GTIN which the Distribution Unit (DU) consists of, the number of Stock Keeping Units (SKU) batch / lot number and shelf life information if applicable.
SSCC is the most important key for traceability of Distributions Units (DU), see Recommended way to track and trace a product in the value chain.
For that reason SSCC shall not be reused until after a minimum of 6 years.
Recommended way to track and trace a product in the value chain
Efficiency and traceability are achieved primarily through:
- Synchronization of product information between the various parts in the value chain.
The purpose is for all players to obtain correct and coherent product information about the products. Between suppliers and retail chains in the Norwegian groceries sector the EPD database is used for the registration, quality assurance and distribution of product information.
- Electronic Data Interchange (EDI) between the actors.
The purpose is to reduce manual operations and reduce lead time in the value chain. The most widely used EDI messages are order, order confirmation, Despatch Advice and invoice.
- Standardized labelling of outer packaging.
The purpose is to contribute to faster and more efficient shipping, distribution and receipt of the products. A common labelling concept for the grocery industry is used here; GS1-128.
To ensure rational product and information flow in the distribution chain, STAND recommends a uniform labelling of Stock Keeping Units (SKU) and Distribution Units (DU).
This simplifies the labelling of the manufacturer / supplier, shipment by shipper / freight forwarders and merchandise at distributor / store.
This labelling concept also applies to types of transport units other than pallets.
For fish and fish products, the following applies:
STAND has decided to refer to Norwegian Standard NS17099:2020 “Information technology — Fishery and aquaculture products — Requirements for labelling of distribution units and pallets in the trade of fishery and aquaculture products” for products that fall under this category. This standard replaces todays NS9405: 2014 “Fish and fish products. Requirements for labelling of distribution units and pallets in the trade of fish and fish products», and is valid as from 30. September 2020.
It can be ordered from Standard Norway.
Product information on Stock Keeping Unit (SKU), with example of Stock Keeping Unit (SKU) label
Only product information should be labelled on a Stock Keeping Unit (SKU).
What information to be labelled depends on the type of product.
Intermediate Cartons shall be labelled as Stock Keeping Units (SKU)
Possible product information which SHALL or CAN be labelled on a Stock Keeping Unit (SKU)
GTIN – Global Trade Item Number
Includes GTIN-8 (8 digits), GTIN-12 (12 digits), GTIN-13 (13 digits) and GTIN-14 (14 digits).
All Stock Keeping Units (SKU) must have their own GTIN.
– For variable measure Stock Keeping Units (SKU), GTIN-14 with a leading digit 9 should be used.
– For other products, GTIN-13 is recommended.
Name of brand owner
– shall be shown in plain text either on the label or on the packaging.
Product name
– Must be written in plain text on the Stock Keeping Unit (SKU) product label.
– Must be based on the text in the Norwegian grocery data pool – EPD database, and consists of product name, attributes, – and product description.
– The product description labelled on the Stock Keeping Unit (SKU) must be identical to the text in the Despatch Advice and Invoice.
-Product description should also contain a package description: for example, Coffee 12 x 500gr.
Batch / lot number
– A number generated by the manufacturer, used to achieve full traceability of product lot/batches in the value chain
– GS1-128 AI 10 must be used.
Shelf life information (“Best before” date, alternatively “Expiry date”)
– Must be labelled on all Stock Keeping Units which has shelf life printed on the Consumer Unit (CU)
GS1-128 AI 15 shall be used for «Best before date”
GS1-128 AI 17 shall be used for «Expiry date»
Net weight
– GS1-128 AI 3103 shall be used for variable measure Stock Keeping Units (SKU).
– Net weight means weight of product excluding packaging (the same weight that is being invoiced).
Supplier’s item number
– can be labelled in plain text.
Table showing what SHALL or CAN be labelled:
Overview of product information that shall or may be labelled on Stock Keeping Unit (SKU): | ||||
Information | Human readable text | GS1-128 (bar code) | AI | Format |
GTIN for Stock Keeping Unit (SKU) | Must be labelled | Must be labelled | 01 | n2 + n14 |
Name of brand owner | Must be labelled | Not labelled | ||
Product name | Must be labelled | Not labelled | ||
Batch / lot number | Must be labelled | Must be labelled | 10 | n2 + an..20 |
Shelf life | Must be labelled if shelf life is marekd on the Consumer Unit (CU) |
Must be labelled if shelf life is marekd on the Consumer Unit (CU) |
15, alternatively 17 |
n2 + n6
|
Net weight | Must be labelled for products with variable measures |
Must be labelled for products with variable measures |
310x | n4 + n6
|
Supplier’s item no. | Can be labelled | Not labelled | ||
Example of GS1 Product label for Stock Keeping Unit (SKU), for a product with “Best before” date and a fixed weight:
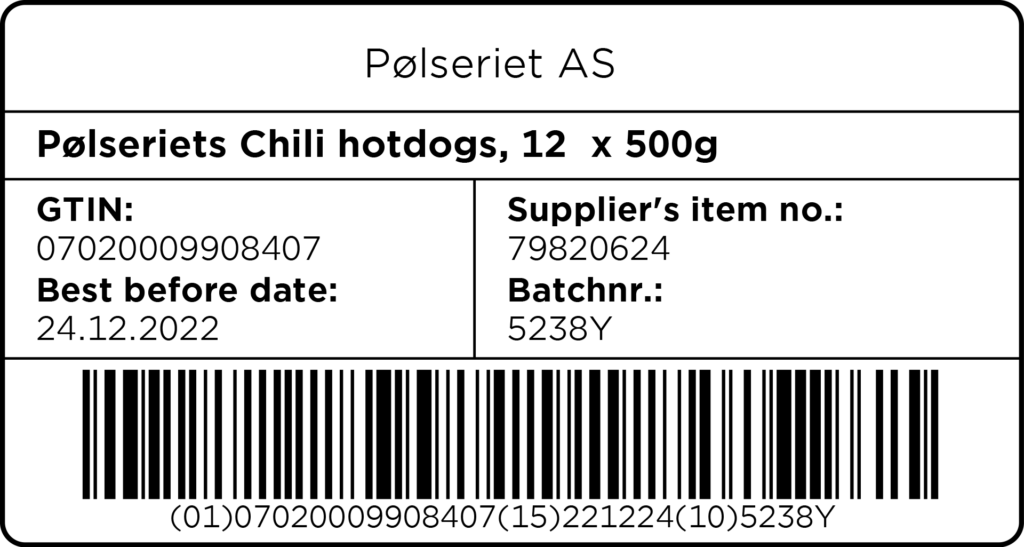
Example of GS1 Product label for Stock Keeping Unit (SKU), for a product with “Expiry date” and variable measures:
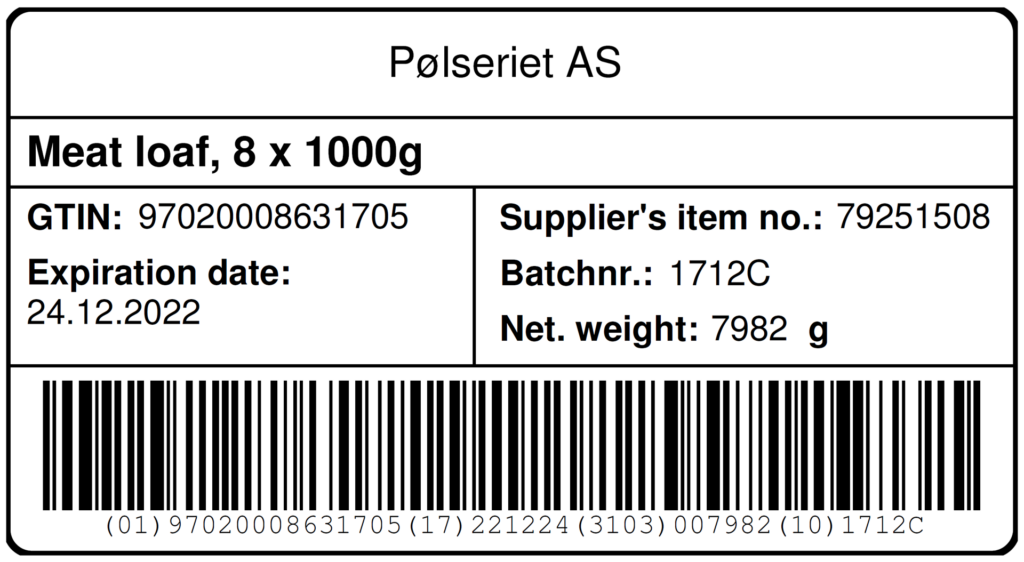
Guidelines for labelling of Stock Keeping Units (SKU)
Type of bar code symbol
When labelling with bar code on Stock Keeping Units (SKU) GS1-128 bar code shall be used.
Identical information
Same information (GS1-128 AI) should only occur once per label.
Size and design of labels
Since the shape and size of the Stock Keeping Units (SKU) is highly varied, size and design of the label may also vary.
Quality of labels
It is a prerequisite that the labels are readable throughout the value chain for the entire life span of the unit. Therefore, the quality of GS1-128 bar codes must minimum fulfill print quality with “Grade C” according to standard ISO / IEC 15416.
To achieve “Grade C” when reading, “Grade B” or better is recommended at printing.
Quality of labels and bar codes can be verified at GS1 Norway.
Placement of labels on Stock Keeping Units (SKU)
It is recommended that the Stock Keeping Units (SKU) is labelled on two sides.
If labelling can only be done on one side, the label on the Stock Keeping Unit (SKU) must be on the same side as one of labels on the pallet (consistent orientation).
By column stacking the Stock Keeping Unit (SKU) label will be oriented towards one pallet label (either on the short or long side of the pallet).
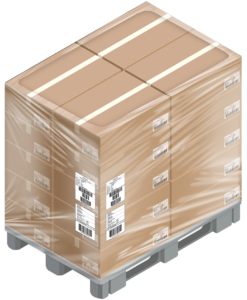
By bond stacking (like bricks) the Stock Keeping Unit (SKU) label could be oriented towards the two labels of the pallet. That is, both on the short and the long side of the pallet.
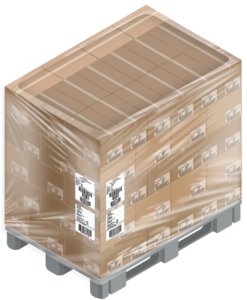
Bar codes
The following recommendations apply to GS1-128 bar code symbols:
- The orientation of the bar code should be such that the bars are vertical (picket fence).
- Size factor is in the range of 25 to 94% of nominal size.
- The minimum bar code height is 13 mm.
- Minimum 5 mm height on human readable text.
- The location of the bar code should be such that the bottom of the bar code is about 32 millimeters from the bottom of the Stock Keeping Unit (SKU).
- The bar code symbol included quiet zone (margins), must be at least 19 millimeters from a vertical edge to avoid damage to the label.
- If the height of the Stock Keeping Unit (SKU) is less than 50 mm, the bar code should be placed as high as possible and information to be written in plain text can be placed to the left of the bar code
Placement of bar code symbols on the Stock Keeping Unit (SKU)
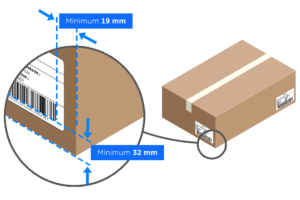
Placement of bar code symbols on Stock Keeping Units (SKU) with height less than 50 mm
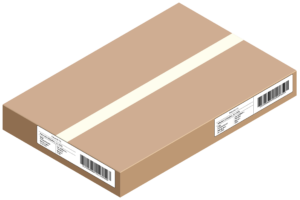
Product information on Distribution Unit (DU), with example of Distribution Unit (DU) label
The standard differs on different types of pallets depending on the content.
Only Standard pallet and Promotional Unit can provide a clear labelling of product information that applies to the entire pallet.
Standard pallet
A Distribution Unit (DU) containing the same product (same GTIN) with fixed count of Stock Keeping Units (SKU) and where labelling of unique product information on the Distribution Unit (DU) is possible.
It is recommended that a Standard pallet only contain Stock Keeping Units (SKU) with the same batch / lot number and shelf life date.
There are two different types of Standard pallet:
- Standard pallet with height 120 cm
- Standard pallet with height 60 cm (Standard Pallet – Low)
Standard pallet – Low is used for low-frequency products and for products with short shelf life.
A product can only be used on one type of Standard pallet, either 120 cm height or 60 cm height.
Standard pallet with height 120 cm
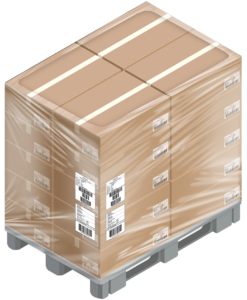
Standard pallet with height 60 cm (Standard pallet – Low)
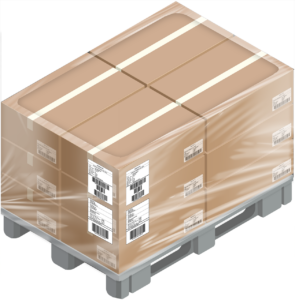
Standard pallet shall be labelled with product and transport information.
Since product information and transportation information are usually known at different times, the practical solution is to label the device with two different labels:
- Product information label (incl. SSCC)
- Label with transport information
Product information on the GS1 product label for Standard pallet
SSCC (License Plate)
Must be labelled with GS1-128 AI 00 on the GS1 Product label on each Standard pallet in human readable text and in the bar code. The SSCC provides a unique identification of each Distribution Unit (DU). Because of traceability a SSCC shall not be reused until after a minimum of 6 years.
The bar code containing the SSCC should be the lowest bar code on the label. It is recommended to have a bar code containing only the SSCC and no other AI’s.
GTIN – Global Trade Item Number
Standard pallet must be labelled with GTIN. This can be done in the following ways:
- Primarily, GTIN for the Stock Keeping Unit (SKU) should be used
- GS1-128 AI 02 must be used. The count of Stock Keeping Units (SKU) is also required on the Distribution Unit (DU) using GS1-128 AI 37
- The Distribution Unit’s (DU) own unique GTIN can also be used, using GS1-128 AI 01.
Product name
The product’s name must be written in human readable text on the Distribution Unit’s (DU) product label. Product name must be based on the text in the Norwegian grocery data pool – EPD database, and consists of product name, attributes, and product description. The product description labelled on the Distributions Unit (DU) must correspond to the text in the Despatch Advice and the invoice.
Batch / lot number.
GS1-128 AI 10 is generated by the manufacturer and used to track the product back to specific production series.
If all Stock Keeping Units (SKU) on the pallet have the same batch / lot number, this is indicated on the label in human readable text and bar code. If the pallet contains Stock Keeping Units (SKU) with different batch / lot numbers, batch / lot number is omitted on the label. However, all unique batch / lot numbers must be stated in the electronic Despatch Advice.
Shelf life information
GS1-128 AI 15 should be labelled on all Distribution Units (DU) that contain Consumer Unit (CU) with “Best before date” printed on them.
Alternatively, the expiration date (GS1-128 AI 17) may be used for shelf life marking.
Net weight (in grams)
GS1-128 AI 3103 shall be used for variable measure products. Net weight means weight of product excluding packaging (the same weight that is being invoiced).
Gross weight (in whole kg)
Shall be labelled in human readable text on each Distribution Unit (DU). Gross weight means weight of products, packaging and pallet (load carrier).
Max. top load (in whole kg)
Must be labelled in human readable text.
Distribution Units (DU) that can not be stacked (in transport or storing) are marked with: Cannot be stacked (Kan ikke stables).
Temperature requirements
shall be labelled in human readable text if the product has a temperature requirement.
Product labelling on Standard pallet
Overview of product information that shall or may be labelled on Standard pallet: | ||||
Information | Human readable text | GS1-128 (bar code) | AI | Format |
SSCC (License Plate)1) | Must be labelled | Must be labelled | 00 | n2 + n18 |
GTIN for the Distribution Unit (DU)2) | Can be labelled | Can be labelled | 01 | n2 + n14 |
GTIN for the contained Stock Keeping Units (SKU) | Must be labelled | Must be labelled | 02 | n2 + n14 |
Count of Stock Keeping Units (SKU) on the DU | Must be marked except when DU is defined as an SKU | Must be marked except when DU is defined as an SKU | 37 | n2 + n..8 |
Product name | Must be labelled | Not labelled | ||
Batch / lot number3) | Must be labelled | Must be labelled | 10 | n2 + an..20 |
Best before date4) | Must be labelled if Consumer Unit (CU) has printed best before date | Must be labelled if Consumer Unit (CU) has printed best before date | 15 | n2 + n6 |
Net weight | Must be labelled for products of variable measure | Must be labelled for products of variable measure | 3103 | n4 + n6 |
Gross weight | Must be labelled | Can be labelled | 3300 | n4 + n6 |
Max. top load | Must be labelled | Not labelled | ||
Temperature requirements | Must be labelled if the product has temperature requirements | Not labelled | ||
1) SSCC shall be indicated on the product label but permitted on both labels provided that the same number is used. 2) Can be used in a case for a transitional period. 3) If Batch / Lot No. is omitted on the Stock Keeping Unit (SKU), or it is different Batch / Lot No. on the Stock Keeping Units (SKU) this should not be labelled on the Distribution Unit (DU). 4) Alternatively, the expiration date (GS1-128 AI 17) may be used for shelf life marking. |
Example on the GS1 product label for Standard pallet
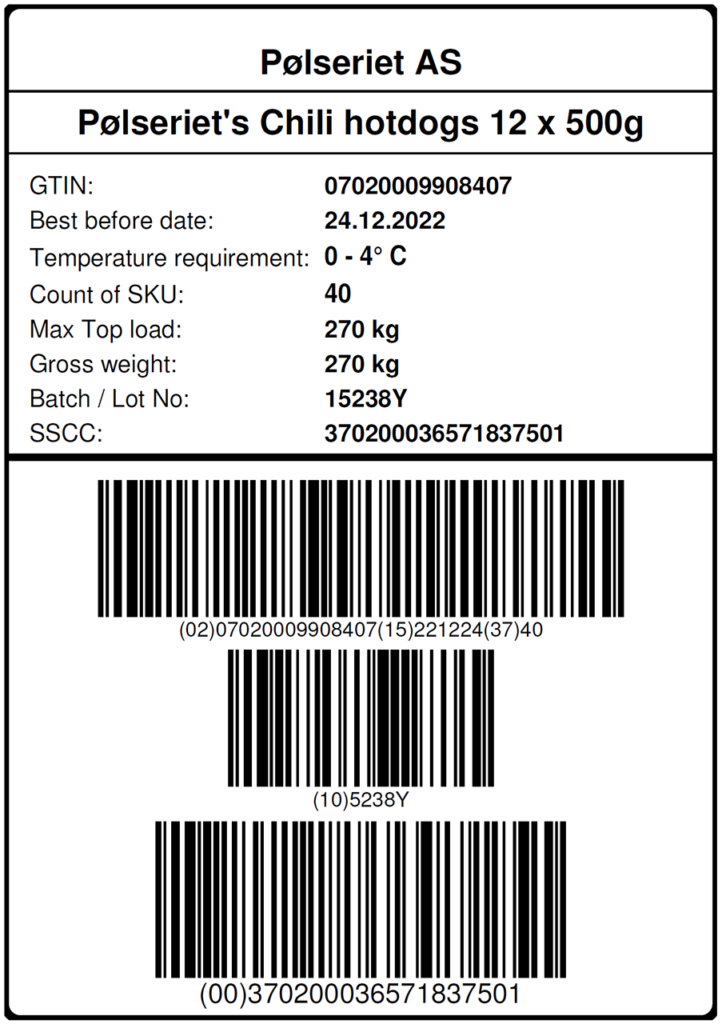
Promotional Unit
A Unit defined as a Stock Keeping Unit (SKU) containing a fixed number of Consumer Unit (CU), intended for display in stores.
Promotional Unit can be 1/1 pallet, 1/2 pallet or 1/3 pallet.
Each Promotional Unit has its own load carrier.
Promotional Unit consisting of 1/2 pallet or 1/3 pallet are placed on a slave pallet. This constitutes a transport unit.
If slave pallet is omitted, this must be agreed bilaterally. For example, for 1/2 pallets with good stability, they can be tied together and exclude the slave pallet. This allows for better use of the pallet by increasing the Promotional Unit, thus allowing more items on the pallet.
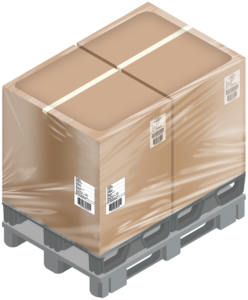
Promotional Units are labelled with two levels of SSCC:
- At the lowest level is labelled with Product label for Promotional Unit as a Stock Keeping Unit (SKU) with the addition of SSCC. The product label is labelled on each Promotional Unit.
- The whole Promotional Unit is labelled with Standard shipping label for the groceries sector. If the Promotional Unit is a 1/1 pallet, this is labelled as a Standard pallet.
Labelling of Promotional Units provides increased traceability in the value chain
Product information on the GS1 product label for Promotional Unit
SSCC (License Plate)
Must be labelled with GS1-128 AI 00 on the GS1 Product label on each Promotional Unit in human readable text and in the bar code. The SSCC provides a unique identification of each Distribution Unit (DU). Because of traceability a SSCC shall not be reused until after a minimum of 6 years.
The bar code containing the SSCC should be the lowest bar code on the label. It is recommended to have a bar code containing only the SSCC and no other AI’s.
GTIN – Global Trade Item Number
Promotional Unit must be labelled with GTIN. This can be done in the following ways:
- Primarily, GTIN for the Stock Keeping Unit (SKU) should be used
- GS1-128 AI 01 must be used
Product name
The product’s name must be written in human readable text on the Distribution Unit’s (DU) product label. Product name must be based on the text in the Norwegian grocery data pool – EPD database, and consists of product name, attributes, and product description. The product description labelled on the Distributions Unit (DU) must correspond to the text in the Despatch Advice and the invoice.
Batch / lot number
GS1-128 AI 10 is generated by the manufacturer and used to track the product back to specific production series.
If all Stock Keeping Units (SKU) on the Distribution Unit (DU) have the same batch / lot number, this is indicated on the label in plain text and bar code. If the Distribution Unit (DU) contains Stock Keeping Units (SKU) with different batch / lot numbers, batch / lot number is omitted on the label. However, all unique batch / lot numbers must be stated in the electronic Despatch Advice.
Shelf life information
GS1-128 AI 15 should be labelled on all Distribution Units (DU) that contain Consumer Unit (CU) with “Best before date” printed on them.
Consumer Unit (CU). Alternatively, the expiration date (GS1-128 AI 17) may be used for shelf life marking.
Net weight (in grams)
GS1-128 AI 3103 shall be used for variable measure Stock Keeping Units (SKU). Net weight means weight of product excluding packaging (the same weight that is being invoiced).
Gross weight (in whole kg)
shall be labelled in human readable text on each Distribution Unit (DU). Gross weight means weight of products, packaging and pallet (load carrier).
Max. top load (in whole kg)
must be labelled in human readable text.
Distribution Units (DU) that can not be stacked (in transport or storing) are marked with: Cannot be stacked.
Temperature requirements
shall be labelled in human readable text if the product has a temperature requirement.
Product labelling on Promotional Unit
Overview of labelling of product information that may or may not be labelled on Promotional Unit: | ||||
Information | Human readable text | GS1-128 (bar code) | AI | Format |
SSCC (License Plate) | Must be labelled | Must be labelled | 00 | n2 + n18 |
GTIN for Stock Keeping Unit (SKU) | Must be labelled | Must be labelled | 01 | n2 + n14 |
Product name | Must be labelled | Not labelled | ||
Batch / lot number1) | Must be labelled | Must be labelled | 10 | n2 + an..20 |
Best before date2) | Must be labelled if Consumer Unit (CU) has printed best before date | Must be labelled if Consumer Unit (CU) has printed best before date | 15 | n2 + n6 |
Temperature requirements | Must be labelled if the product has temperature requirements | Not labelled | ||
Supplier’s item number | Must be labelled | Not labelled | ||
1) If Batch / Lot No. is omitted on the Stock Keeping Unit (SKU), or it is different Batch / Lot No. on the Stock Keeping Units (SKU) this should not be labelled on the Distribution Unit (DU). 2) Alternatively, the expiration date (GS1-128 AI 17) may be used for shelf life marking. |
Example of Stock Keeping Unit (SKU) label with SSCC for Promotional Unit
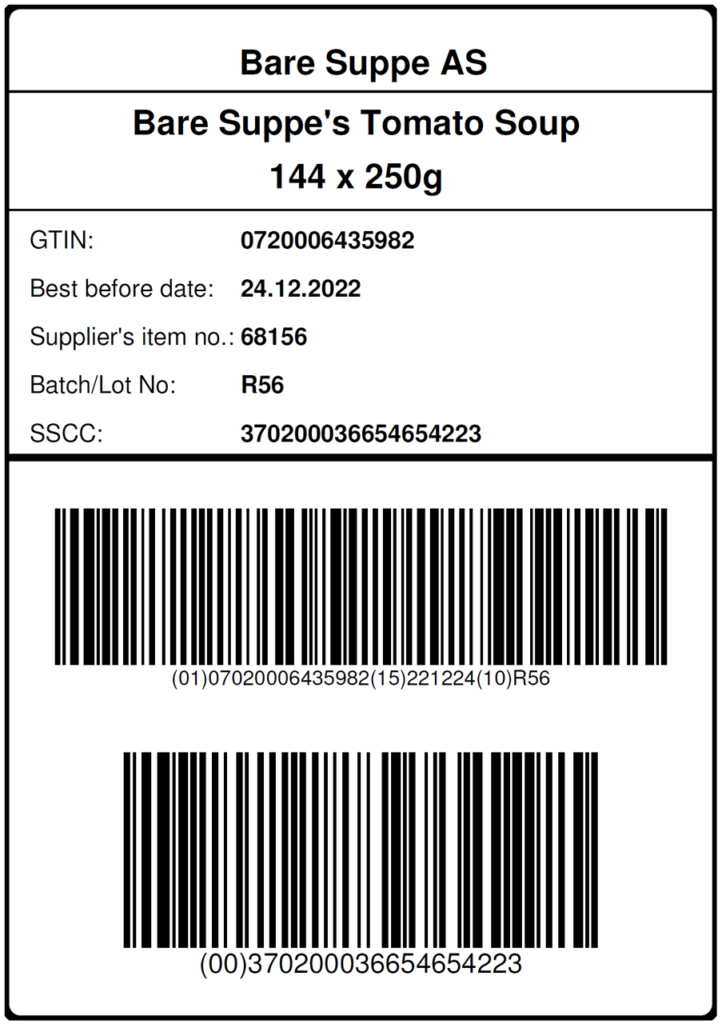
Units where product information can not be entered on their own label
Mixed pallet
Two variants of Mixed pallets are described; with and without intermediate pallet.
On Mixed pallet it is not possible to enter product information on its own label.
Mixed pallet without intermediate pallet:
Pallet consisting of several different products.
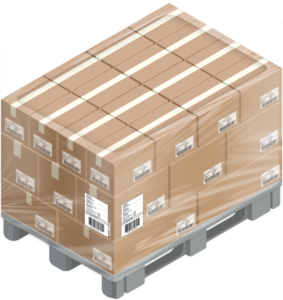
Mixed pallet with intermediate pallet:
Pallet consisting of several different products, where each product is stacked in one or more layers, and where each different product is separated by an intermediate pallet.
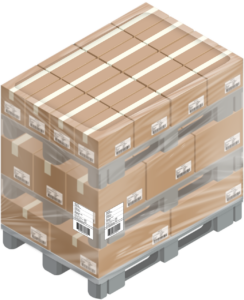
The choice of type of mixed pallet depends, among other things, on handling costs, transport / environmental costs and storage technology and must be agreed bilaterally between the parties.
Packaging and stability of the Stock Keeping Unit (SKU) must be considered when choosing type of a Mixed pallet.
If intermediate pallet(s) are used, it shall always be ordered the amount of Stock Keeping Units (SKU) to complete a layer.
Mixed pallet (both with and without intermediate pallet) is labelled with Standard shipping label for Norwegian grocery sector.
Customer packed pallet
When a supplier assembles products for delivery to the final recipient, the products are packaged and labelled with SSCC at two packaging levels.
Customer packed units are labelled for delivery to the end-user and the Distribution Unit (DU) is labelled for delivery to the transit warehouse.
On Customer packed units it is not possible to enter product information on the Distribution Unit (DU) label.
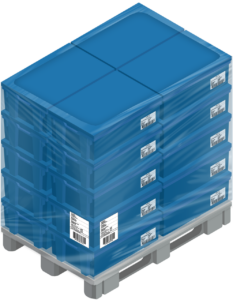
A customer-packed pallet can be Customer packed unit – multiple route, multiple customers, Customer packed unit – single route, multiple customers, or Customer packed unit – single customer.
- Customer packed unit – multiple route, multiple customers is a unit of products for two or more end recipients that will be split in transit storage.
- Customer packed unit – single route, multiple customer is a unit of products for two or more end recipients on the same route or transport.
- Customer packed unit – single customer is a unit of products that are intended for only one end recipient.
This Customer packed units does not need to have its own load carrier and is being loaded on a standardized transport unit (for example, an EUR pallet).
Customer packed unit – multiple route, multiple customers and Customer packed unit – single route, multiple customer is stacked in columns per. end receiver.
Customer packed unit – multiple route, multiple customers is split after products receipt in the transit warehouse, and the individual Customer packed unit is forwarded to the final recipient. A prerequisite is that all Customer packed units located on one Distribution Unit (DU) are destined for the same transit warehouse.
Transport information on pallet with example of transport label
Content of the Standard shipping label for the Norwegian grocery sector.
Overview of labelling of Standard shipping label: | ||||
Information | Human readable text | GS1-128 (bar code) | AI | Format |
Sender’s name, street address, postal code, city | Must be labelled | Not labelled | ||
Recipient’s name, street address, postal code, city | Must be labelled | Not labelled | ||
Name, address, etc. for the Crossdocking terminal | Must be labelled when the delivery is via the Crossdocking terminal | Not labelled | ||
Buyer’s reference | Must be labelled | Not labelled | ||
Gross weight | Must be labelled | Can be labelled | 3300 | n4 + n6 |
Max. Top load1) | Must be labelled | Not labelled | ||
Temperature requirements | Must be labelled | Not labelled | ||
SSCC (License Plate) | Must be labelled | Must be labelled | 00 | n2 + n18 |
1) Max Top load is omitted for Mixed pallet. |
Example of Standard shipping label for the grocery industry
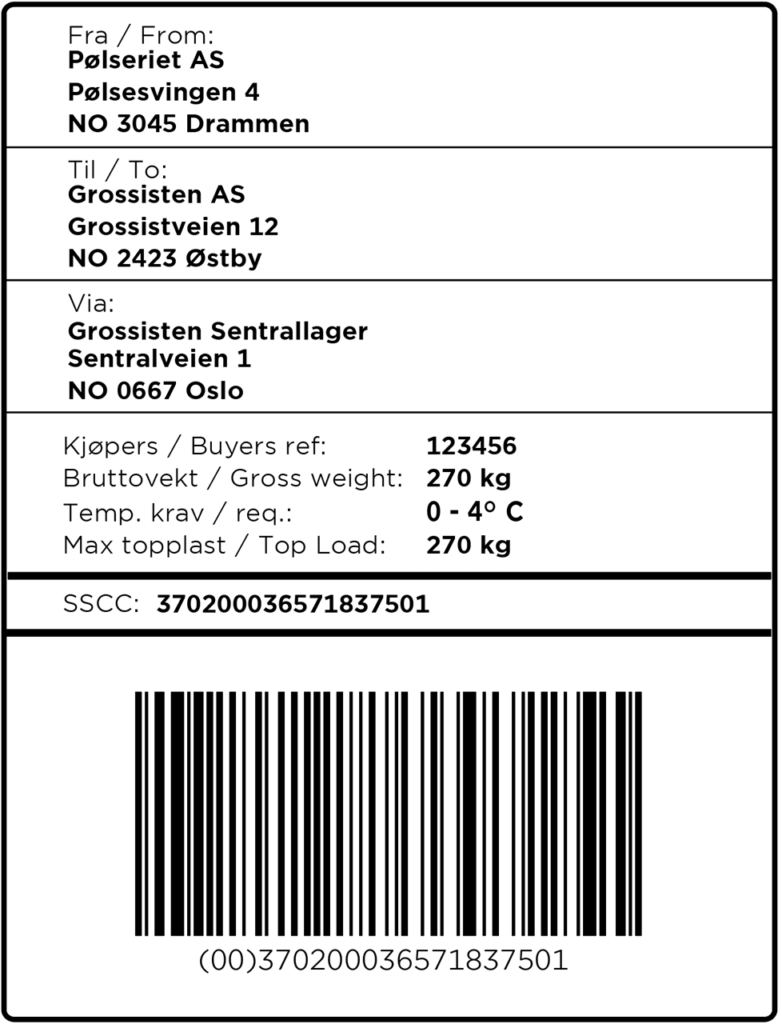
Transport label for Standard pallet
Standard pallet is labelled with Standard shipping label for the grocery industry
A GS1 product label on a Standard pallet requires labeling of SSCC, gross weight, top load weight and temperature requirements.
This information can therefore be omitted from Standard shipping label for the grocery industry.
If both product label and transport label are used, SSCC can be labelled on both labels provided that the identical number is used.
Transport label for Promotional Unit
The Distribution Unit (DU) containing one or more Promotional Units is labelled with Standard shipping label for the grocery industry.
The Distribution Unit (DU) is identified and labelled with its own SSCC
If the Promotional Unit a 1/1 pallet, the same labelling of transport label as for Standard pallet is used.
Transport label for Mixed pallet
Mixed pallet (both with and without interlayer pallet) is labelled with Standard shipping label for the Norwegian grocery industry.
If the Mixed pallet is not stackable, information on Top load is omitted.
Transport label for Customer packed pallets
The Customer packed pallet is labelled with Standard shipping label for the grocery industry.
Note in particular:
Recipient’s name, address, etc.
As recipient transit warehouse is given and transit address is given as delivery address. The pallet must be labelled with the transit warehouse’s name, street address, postal code and postal address in human readable text.
Name, address, etc. for the distribution warehouse.
The via-field the distribution warehouse is given. The pallet must be labelled with the distributions warehouse’s name, street address, postal code and postal address in human readable text.
Transport label for Customer packed units
Transport Information.
On this label, a separate field has been created for transport information. This is information that the buyer sends to the supplier in his order and which the supplier must put on the Customer packed unit’s transport label.
Format and content of transport information is agreed between the parties.
Content in transport label for customer packed unit
Transport label for customer packed unit: | ||||
Information | Human readable text | GS1-128 (bar code) | AI | Format |
Sender’s name, street address, postal code, city | Must be labelled | Not labelled | ||
End recipients’s name, street address, postal code, city | Must be labelled | Not labelled | ||
Name, address, etc. for the transit warehouse1) | Must be labelled | Not labelled | ||
Transport information2) | Must be labelled | Not labelled | ||
Buyer’s reference3) | Must be labelled | Not labelled | ||
Gross weight4) | Must be labelled | Can be labelled | 3300 | n4 + n6 |
Temperature requirements | Must be labelled | Not labelled | ||
SSCC Code (licence plate) | Must be labelled | Must be labelled | 00 | n2 + n18 |
1) Transit Warehouse where the pallet is split/cross-docked, is stated in the VIA-field | ||||
2) Transport information is agreed between the parties | ||||
3) Example The Customers Ordering Number | ||||
4) Gross weight is the sum of weight of the products, packaging materials and pallet (load carrier) |
Example of shipping label for Customer packed unit
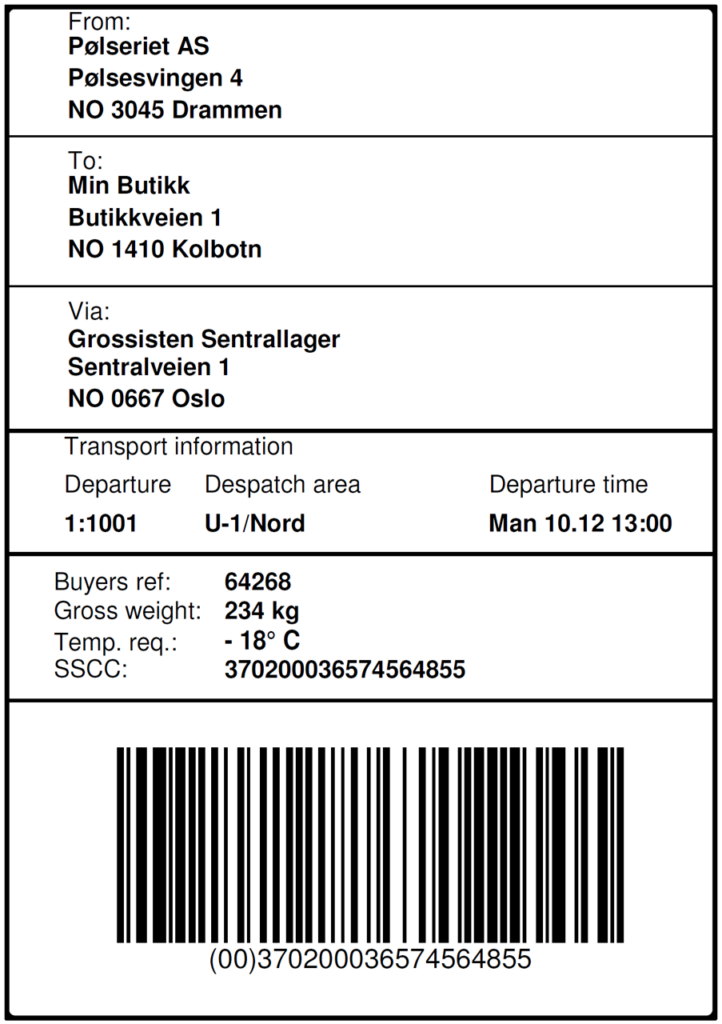
Guidelines for labels on Distribution Units (DU)
Placement of labels on pallet
Two types of labels shall be used; label for product information and label for transport information.
- The minimum requirement is that the pallet should be labelled on two sides with both label types; one of the short sides of the pallet and the right hand long side (seen from the short side).
- Product and transport label must be on the same side of the pallet.
- When multiple labels are used on the same side of the pallet, the labels should be placed underneath each other. The label that contains SSCC placed at the bottom.
- The labels should be placed so that the bottom of the lowest bar code should be at least 400 mm above the floor, and the top of the uppermost bar code should not be more than 800 mm above the floor.
- The label should be placed at least 50 mm from the vertical edge.
- For pallets lower than 400 mm the labels should be placed as high as possible.
- If all information is known at the time the pallet is labelled and there is space on the label, all information can be labelled on one single label.
- To ensure automatic reading of the bar codes Promotional Units, Customer packed pallet and Mixed pallet should only the transport label on the transport unit be readable
- Product label on Standard pallet with height 60 cm (Standard pallet – Low) should be placed as high as possible.
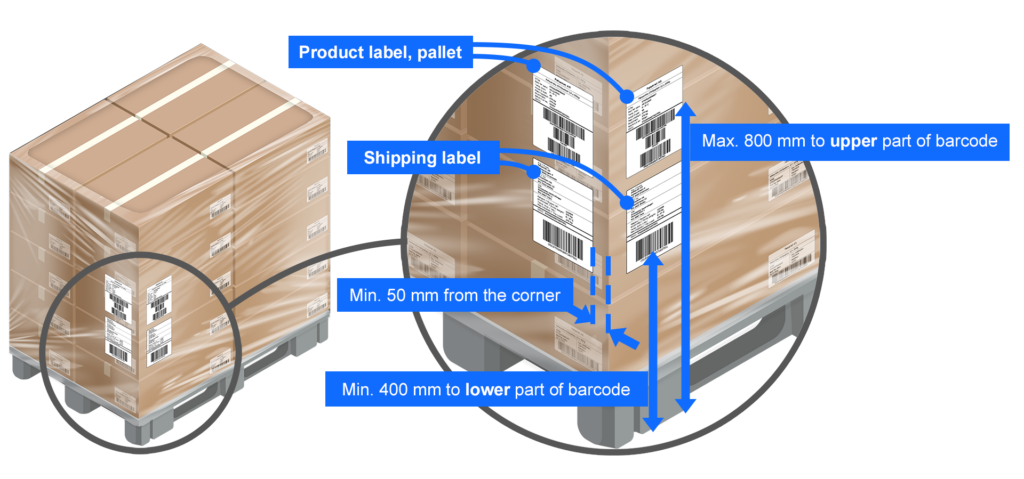
Identical information
Same information (GS1-128 AI) shall only appear once on the product and transport label.
This means in practice that the same information can not be repeated on the same label or that the same information may appear on multiple labels on the device (pallet).
The exception is SSCC which is allowed on both labels if it is an identical number used.
Size and design of the labels
The following recommendation applies:
- The width of the label should be 105 mm or 148 mm
- The height of the label may vary
Recommended formats are:
- A5 (148mm x 210mm)
- A6 (105mm x 148mm)
- 105 mm x 192 mm
Quality of labels
- It is a prerequisite that the labels are readable throughout the value chain for the entire life span of the unit
- It is a requirement that the quality of GS1-128 bar codes minimum meets print quality with “Grade C” according to Standard ISO / IEC 15416.
To achieve “Grade C” when reading, “Grade B” or better by printing is recommended - When affixing the labels, it is important to ensure that the bars in the GS1-128 symbol are correct and unbroken (avoid “wrinkling” on the label).
Bar code requirements for labelling with GS1-128 on Distribution Units (DU)
Bar code label with GS1-128 bar codes shall be done according to GS1 General Specifications Chapter 5.4.
Note in particular:
- Size factor is in the range of 50 to 94% of nominal size.
- The minimum bar code height is 32 mm.
- When labelling GTIN (AI 01 and AI 02) always use 14 digits.
When GTIN has 13 digits, you must enter a leading 0 (ex. 07038010000065). - For bar code labelling with GS1-128, a separator, called Function Code 1 (FNC1), is used between the individual information elements (AI’s).
This applies except for the AI’s that have predefined fixed length.
The following AI’s in this document have predefined length AI 00, AI 01, AI 02, AI 15. - It is recommended to have the AI’s to be followed by FNC1 at the end of the bar code, as the FNC1 code may be omitted.
- It is important to the requirements for quiet zone (margins) to be adhered to.
At size factor 50%, the right and left quiet zone margin is 5 mm, and at the size factor 94% the quiet zone margins are 9.4 mm.
Checklist for optimization of Consumer Unit (CU), Stock Keeping Unit (SKU) and Distribution Unit (DU)
The checklist is a declaration that the standard is complied with
Endringslogg
Determine total shelf life of a product and requirements for labelling this
The responsibility for determining type of shelf life labelling and total shelf life lies with the manufacturer. The shelf life is calculated from the time the product is ready for sales, for example from after the product has been matured and checked.
The actual shelf life of the product is affected by a variety of conditions, primarily the properties of the raw material and the external impact.
The manufacturers are encouraged to assess whether dynamic shelf life labelling can be practiced.
This means that total shelf life can be expanded when conditions allows for this to be done.
The number of days marked on a product may therefore be more than the number of shelf life on selected products.
According to the Mattilsynet (Norwegian Food Safety Authority), the use of dynamic shelf life is within the current regulations.
Labelling
The packaging (Consumer Units (CU) and Stock Keeping Units (SKU)) shall be labelled according to the manufacturer’s choice of type of shelf life and total shelf life.
Allocation of total shelf life on a product
Reducing food waste is an overall goal in society. Food waste related to exceeding the limit values of shelf life between the parties in the value chain, constitutes a significant part.
Surveys shows that food waste are significantly reduced if the store and the consumer have a larger part of the total shelf life.
It is therefore a goal that the producer and distributor consume the least amount of available time and that the maximum amount of time is exposed to the consumer.
The grocery industry has defined one Table for allocation of shelf life of a product which regulates the responsibility for and expectations the recipient of products has, linked to shelf life. Online players with b2c sales will be defined as retailers when dividing total shelf life.
In case of minor exceedances of the table’s limit values, participants are expected to seek solutions that provide the lowest possible food waste.
The parties are encouraged to develop performance and collaborate to reduce consumption of shelf life.
Endringslogg
Evaluate the use of dynamic shelf life
“Expiry date overdue” is the main reason for food waste in the value chain. A more flexible shelf life labelling throughout the year could help reduce food waste.
Shelf life is affected by several conditions that may vary. It is possible to specify increased shelf life in periods of time or for batches. This is termed as “dynamic shelf life». In practice, it means that overall shelf life can be expanded when conditions give the opportunity to do so.
The supplier should inform the customer if dynamic shelf life is applied.
According to the Mattilsynet (Norwegian Food Safety Authority), the use of dynamic shelf life within the current regulations: “It is the manufacturer who assesses and puts the shelf life of the food products. Manufacturers know the raw materials and processes used. Shelf life should be based on common and realistic conditions for transportation, storage and sales. This does not prevent manufacturers from taking into account that there may also be different external conditions for the shelf life of the foodstuffs. In practice, manufacturers often put the shelf life out of the most demanding but realistic conditions throughout the year. If the business has full control and overview of the terms, nothing stops them from choosing different shelf life throughout the year for the same product. This means the food is given a shelf life that is adapted to season, temperature and other conditions.”
More information can be found here: http://www.mattilsynet.no/mat_og_vann/merking_av_mat/generelle_krav_til_merking_av_mat/holdbarhetsmerking_paa_matvarer.2711
Examples of using dynamic shelf life that could have longer shelf life than often is the practice today:
- Different temperatures throughout the year
In order to make a realistic assessment, the producer assumes that the products are stored in normal outdoor / room temperature for a shorter period of time through the value chain, such as transshipment, stock refills in stores, consumer carts, transport from store to home and in the home (in and out of the fridge and on the kitchen table). In summer, the outdoor / room temperature is higher and thus has a greater impact on shelf life. To make a realistic assessment, it’s normal to take into account the assumptions in the summer period and determine the shelf life based on this, and the same shelf life is normally used throughout the year.
- Different shelf life based on different technology
Different companies may have different production methods and / or hygiene standards. To make a realistic assessment, the starting point is the technology that provides the shortest shelf life.
- Different shelf life of raw materials
The regulations or internal rules stipulate that raw materials that are up to x days “old” may be used at any given time in the manufacturing process. Then the shelf life is determined by using x-day-old raw material each time. This even though you often use fresher raw materials than x days.
- Different raw material quality
Raw material quality may vary naturally over a year, and in some cases this may affect shelf life. To make a realistic assessment, the raw material with the shortest shelf life is used, and normally uses the same shelf life of the finished foods throughout the year.
Dynamic shelf life and the EPD database
There is no need for any changes to the EPD database to utilize dynamic shelf life.
It is the product’s shortest shelf life during the year the supplier must register in the EPD database.
The establishment of bilateral agreements for the assessment of shelf life
The risk of food waste is related to the remaining shelf life of a product. To avoid food waste, the players in the grocery industry have agreed to exhibit flexibility in the value chain to handle minor deviations in assessment of shelf life. This is done by establish bilateral agreements.
Bilateral agreements will contribute to more flexible assessment of shelf life, thereby reducing food waste in the value chain (manufacturers, distributors, retailers), considering specific and specific conditions, such as geographical distance to customer / market, and volume of sales.
The grocery industry has defined a table for the assessment of total shelf life, based on a three-division between manufacturer, distributor and retailer / consumer. The table prepared for this applies unless otherwise agreed bilaterally.
For products with short shelf life (42 days or less), conditions such as distance to the market and volume of sales will be decisive for determining optimal assessment of shelf life.
- For products with shelf life between 17 and 42 days it is encouraged to consider establish bilateral agreements
- For products with shelf life below 17 days there shall be established bilateral agreements
How to establish bilateral agreements
The assessment of shelf life as stated in the table is the basis for the bilateral agreements.
All parties can initiate bilateral agreements based on expected potential for reduction of total food waste.
Description of how the risk will be shared should be included in the agreements.
Measuring consumed shelf life in the value chain is an instrument for securing facts and monitoring development.
Some examples of situations where it may be appropriate to establish bilateral agreements:
- Deviant date from the table
One example of reducing waste for products with short shelf life is that a supplier in the eastern part of Norway establish a bilateral agreement with a customer regarding a better date than is stated in the table for deliveries to, for example, northern part of Norway, while for example a customer in the middle and western part of Norway receives deliveries according to the table and with the possibility of deviating dates for smaller volumes for deliveries to the southern and eastern part of Norway.
- Divergence date in the beginning of the week
Products delivered at the beginning of a week is quickly reaching the distributor / distribution centre and the retailer before the weekend and is less prone to simple date deviations. Similarly, it is less appropriate to deliver products with “last day according to STAND” or with date deviations on Fridays, if they will not be received by distributor / distribution centre before Sunday evening / Monday.
- Deviant date for promotions
In advance of a promotional period, a delivery agreement with a few day date deviations may be applicable, as these products will have higher turnover than usual for the distributor / distribution centre and at retailers. To reduce the risk of increased drop by lower turnover than usual at the distributor / distribution centre and at retailer at the end of the promotional period, a better date should be provided than indicated in the table.
- Product / value chain specific assessments
Depending on the product / value chain, it may be advisable to redistribute days. For example:
Product with uneven turnover at retailers and / or a lot of waste at retailers.
Here it may be advisable to redefine days from supplier and / or distributor to retail days.
Product with steady turnover at retailers and / or a small amount of food waste.
Here it may be advisable to redefine days from retail and / or distributor to supplier.
Guidelines and routines for tracking, recall and withdrawal
In its framework, STAND has defined guidelines, recommendations and best practices for how products should be marketed in the distribution chain, and how information on this should be exchanged between the parties.
Central to this is the consideration of the consumer and his expectation for safe food.
The guidelines for tracking, recall and withdrawal do not define food quality requirements, but describe what procedures and processes the industry has established to mitigate any unwanted effects should an incident or crisis occur in a product.
Best practices
The guidelines describe best practices in this area.
By following STAND’s framework, the guidelines will be achievable for all parties involved.
Some important prerequisites for best practice.
- Routines and processes must be simple, predictable and intuitive
- Products and deliveries / load carriers must be labeled in a unified, standardized and correct way so that they can be traced through the value chain.
- Product information must be registered in the Tradesolution EPD
- Detailed tracking information must be exchanged digitally between the parties and follow the products through the value chain.
- Action must be taken quickly when an incident or crisis occurs
By ensuring that a total industry complies with STAND’s framework, consumers’ demands and expectations for safe food are fully met.
Objective of the guidelines
The guidelines are aimed at “Contribute to meet consumers’ expectations for safe products”.
Target Audience:
- Anyone who may or will be involved in any recall or withdrawal
- Everyone involved in the production or labeling of products and packaging covered by the guidelines
Products / areas to which the guidelines apply:
- Recommended for food and non-food products, except pharmaceuticals
- Other inputs, plants, animals or foodstuffs
- Materials and articles that are intended to come into contact with, or may affect, inputs or foodstuffs.
Medicines are exempt from the guidelines. Here we refer to separate regulations, not described here.
Certain types of food may be subject to additional regulatory requirements beyond what is described here. An example is the EU’s new tobacco directive (EU 2014/40) which make the requirements for traceability of tobacco products more stringent, but is not described here.
Routines covered by the guidelines
Legislative anchoring of the guidelines
The guidelines are among others based on Norwegian or European regulations on food safety and traceability:
- Product Liability Act of 23 December 1988
- Act on food production and food safety, etc. of 19.12.2003 Matloven (Food Law)
- Regulations on internal control to comply with IK-mat forskriften (IK Food Law)
- EU Food Law (Regulation EC 178/2002)
- Directive 94/62 / EC on packaging and packaging waste
Each party has an obligation to familiarize themselves with the regulations that apply to the products your business sells or are involved in.
The legislation does not impose requirements on how tracking should be performed, and what systems in which tracking information should be recorded. Manual systems may be sufficient as long as the requirements for tracking and tracking information are met.
Routines
The guidelines cover two procedures
- Requirements for and how to design contingency routines
- Implementing actions should an incident or crisis occur
Prepare crisis procedures
This is included:
- Prepare a Risk Analysis
- Prepare a Contingency Plan
- Requirements for product tracking
- Tracking information and labeling requirements
Prepare a Risk Analysis
At the heart of the legislation is the duty of each company to carry out a risk analysis of the health risks the products represent and how the company will relate to this in terms of traceability.
The purpose of the analysis is to reduce / prevent risk through
- Withdrawal of products from the market, or
- Efficient notification or recall of products from consumer
This assumes that the parties are aware of the risks the products may pose and have a preparedness that ensures that they react quickly, correctly and effectively in unwanted incidents. A Risk Analysis should therefore be performed on new products based on an intended relevant incident, so that it can be implemented as quickly as possible should a real incident occur for the product.
The risk analysis consists of three elements that both the government and industry should work on in an equal way:
- Risk Assessment
- Risk Management
- Risk Communication
See more about risk analysis here Design and content of a Risk Analysis.
Prepare a Contingency Plan
If unwanted incidents or crises occur, it is important to be well prepared.
Possible scenarios for what might arise should be thought through and how this should be handled.
A Contingency Plan must be prepared that will allow you to cope with the situation quickly, correctly and effectively. The Contingency Plan must be accurate and accessible to all involved at all times.
The Contingency Plan includes:
- To designate a crisis team, responsible for traceability, recall and withdrawal.
- Internal and external contact lists to quickly reach everyone involved or affected by any incident or crisis
- Training and exercises in the company’s routines and instructions on how to handle incidents or crises. Exercises should be as realistic as possible and carried out with the closest business partner in the value chain
- This must be easily accessible and may consist of, for example
- a brief overview of crisis teams with their roles and responsibilities
- the company’s internal guidelines for handling incidents / crises
- contact lists
- other relevant documentation that is important to have access to should an incident or crisis occur
See more about the Contingency Plan here Design and contents of a Contingency Plan.
Product tracking requirements
The legislation requires that each company must have systems to document which products are purchased from each supplier and which customer has purchased the company’s finished products.
This also includes raw materials and other input that are covered by the legislation.
There is no requirement in the legislation for which type of systems to be used for this.
Businesses can practice more comprehensive tracking systems than the minimum regulatory requirements require, but this is either based on self-imposed requirements or agreements with, and orders from the contracting parties.
Tracking means being able to follow the physical flow of goods. This is often referred to as chain traceability, and assumes that all parties meet the requirements and follow the guidelines for tracking.
Tracking takes into account the legal requirements for all parties to be able to trace their products one step forward and one step back in the value chain.
Tracking one step forward:
This means to the address the products are delivered to.
An invoice system containing information about item number / item name, customer number / customer name and invoice date is sufficient to be able to trace one step forward in the value chain.
If the company is using batch/lot numbers for their products, this should be included in the invoice, despatch advice and the like, or linked directly to the company’s own systems.
Tracking one step backward:
This means the address from which the products are delivered.
The company must keep a log of received products describing which products were purchased from whom and in which quantitiy, and date.
If the addresses for where products are delivered from or delivered to are not in accordance with the legal ownership of the products and the invoice process, this should be agreed separately between the parties.
Requirements for tracking information and labeling
The main purpose of the tracking information is to lay the groundwork for effective blocking, withdrawal or recall of products.
Central tracking information is:
- GTIN (Global Trade Item Number) – Unique identification of products
- GLN (Global Location Number) – Unique identification of trading parties, pick-up points, delivery points etc.
- SSCC (Serial Shipping Container Code) – Unique identification of load carriers / pallets
- Batch / lot number – A unique batch or lot number defined by supplier / manufacturer
- Shelf life – Either Best Before date or Last Consumption Date
It is a requirement that the products are labeled to enable tracking.
The marking must be affixed to the product packaging and legible.
The following applies to finished goods traded between supplier and distributor / retailer:
Information to be marked:
- The name of the supplier
- Product name/description
- Product number identified with a GTIN.
- Best before date / last day of consumption date, if required
- Batch / Lot number, if required
Load carrier (for example pallet) shall be marked with SSCC.
The sender must in his system have an overview of which recipient the product was sent to, and also the recipient must have an overview of which sender the product was received from. Both sender and recipient must be identified with GLN.
Sender shall in his system register:
- Quantity sent
- Shipping Date
- Reception date (if known)
Recipient shall in his system register:
- Quantity received
- Shipping date (if known)
- Reception Date
The following applies to raw materials and other inputs:
- GTIN should be used for identification of inputs / raw material, if available
- GLN should be used for identification of sender / suppliers, if available
More about tracking information and how the product can be tracked in the value chain is described here Recommended traceability methods in the value chain.