Pick up from supplier, transport to distributor / retailer
This sub process describes the requirements, recommendations and guidelines STAND has on how physical delivery is to take place, with the emphasis on the controls to be carried out when taking responsibility for the delivery.
The areas described are:
- Transfer of responsibility for a product at Ex Works delivery terms
- Checks to be performed by the carrier, and possible complaints related to this
- Labelling of transport information and guidelines for labels on Distribution Units (DU)
- Requirements for pallet / palletization on Distribution Units (DU)
- Valid pallets and requirements for these
- Requirements for the design of the Distribution Unit (DU) and palletization
- Placement of Stock Keeping Unit (SKU) on pallet
- The top load labelling system
Transfer of responsibility for products at Ex Works delivery terms
The responsibility for the products is transferred when the seller has made the product available for the buyer in accordance with the agreement.
Unless otherwise agreed, the buyer is responsible for loading of products.
The buyer is liable for any risk of loss or damage to the products from the time the products is placed at the buyer’s disposal.
Check of products at loading, receipt at warehouse, and retailer at Ex Works delivery terms
The buyer or the party acting on behalf of the buyer shall, when the responsibility for the products has been transferred, control the quantity and possible damage to a reasonable extent.
- When loading:
- The number of load carriers and external damage is checked, and whether an exchange or reusable pallet is used.
- Reception at distributor’s warehouse:
- Number of load carriers, external damage, correct product, and if used
exchange or reusable pallet.
Date labelling and number of Stock Keeping Units (SKU) are checked when placed on a stall or pick-up place.
- Number of load carriers, external damage, correct product, and if used
- Reception in store:
- Damage that could not have been discovered when receiving the delivery at the distributor’s warehouse.
Complaints by Ex Works delivery terms
The buyer shall make a complaint about errors or defects in the products within a reasonable time after the error or defect is discovered or should have been discovered.
Seller who claims that the complaint deadline has been exceeded must do so immediately after the complaint has been received.
The buyer may require replacement, redeployment, price reduction, etc. pursuant to the provisions of the applicable law (Kjøpsloven).
All errors and defects must be based on the things that the seller is responsible for.
Transport information on pallet with example of transport label
Content of the Standard shipping label for the Norwegian grocery sector.
Overview of labelling of Standard shipping label: | ||||
Information | Human readable text | GS1-128 (bar code) | AI | Format |
Sender’s name, street address, postal code, city | Must be labelled | Not labelled | ||
Recipient’s name, street address, postal code, city | Must be labelled | Not labelled | ||
Name, address, etc. for the Crossdocking terminal | Must be labelled when the delivery is via the Crossdocking terminal | Not labelled | ||
Buyer’s reference | Must be labelled | Not labelled | ||
Gross weight | Must be labelled | Can be labelled | 3300 | n4 + n6 |
Max. Top load1) | Must be labelled | Not labelled | ||
Temperature requirements | Must be labelled | Not labelled | ||
SSCC (License Plate) | Must be labelled | Must be labelled | 00 | n2 + n18 |
1) Max Top load is omitted for Mixed pallet. |
Example of Standard shipping label for the grocery industry
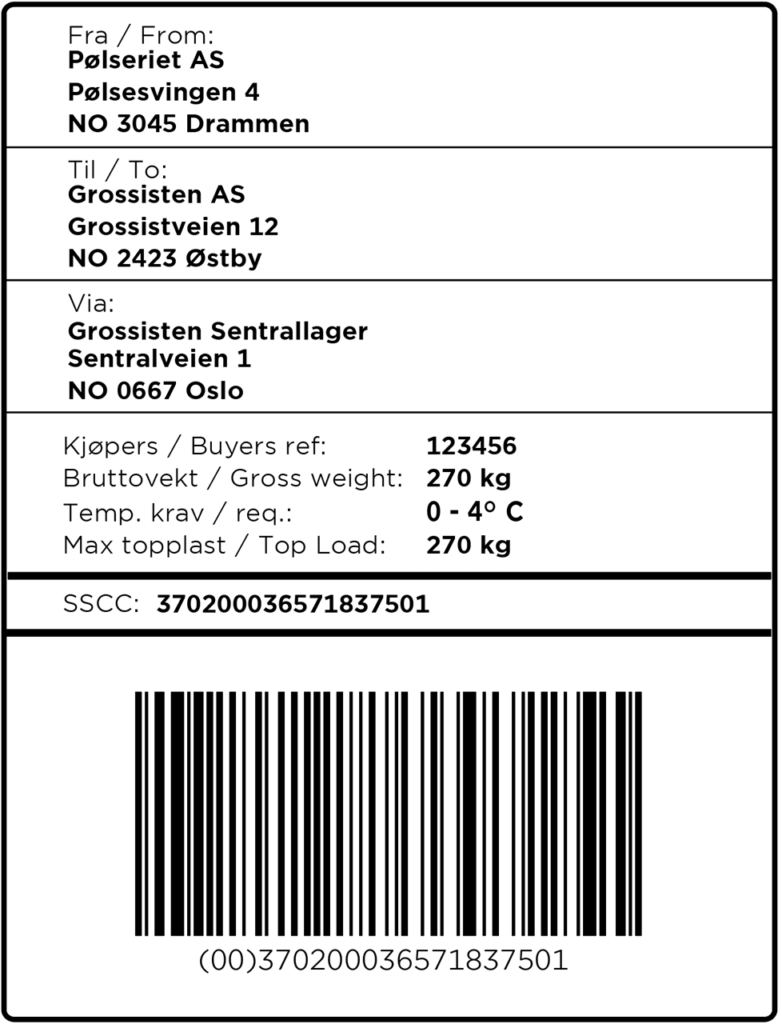
Transport label for Standard pallet
Standard pallet is labelled with Standard shipping label for the grocery industry
A GS1 product label on a Standard pallet requires labeling of SSCC, gross weight, top load weight and temperature requirements.
This information can therefore be omitted from Standard shipping label for the grocery industry.
If both product label and transport label are used, SSCC can be labelled on both labels provided that the identical number is used.
Transport label for Promotional Unit
The Distribution Unit (DU) containing one or more Promotional Units is labelled with Standard shipping label for the grocery industry.
The Distribution Unit (DU) is identified and labelled with its own SSCC
If the Promotional Unit a 1/1 pallet, the same labelling of transport label as for Standard pallet is used.
Transport label for Mixed pallet
Mixed pallet (both with and without interlayer pallet) is labelled with Standard shipping label for the Norwegian grocery industry.
If the Mixed pallet is not stackable, information on Top load is omitted.
Transport label for Customer packed pallets
The Customer packed pallet is labelled with Standard shipping label for the grocery industry.
Note in particular:
Recipient’s name, address, etc.
As recipient transit warehouse is given and transit address is given as delivery address. The pallet must be labelled with the transit warehouse’s name, street address, postal code and postal address in human readable text.
Name, address, etc. for the distribution warehouse.
The via-field the distribution warehouse is given. The pallet must be labelled with the distributions warehouse’s name, street address, postal code and postal address in human readable text.
Transport label for Customer packed units
Transport Information.
On this label, a separate field has been created for transport information. This is information that the buyer sends to the supplier in his order and which the supplier must put on the Customer packed unit’s transport label.
Format and content of transport information is agreed between the parties.
Content in transport label for customer packed unit
Transport label for customer packed unit: | ||||
Information | Human readable text | GS1-128 (bar code) | AI | Format |
Sender’s name, street address, postal code, city | Must be labelled | Not labelled | ||
End recipients’s name, street address, postal code, city | Must be labelled | Not labelled | ||
Name, address, etc. for the transit warehouse1) | Must be labelled | Not labelled | ||
Transport information2) | Must be labelled | Not labelled | ||
Buyer’s reference3) | Must be labelled | Not labelled | ||
Gross weight4) | Must be labelled | Can be labelled | 3300 | n4 + n6 |
Temperature requirements | Must be labelled | Not labelled | ||
SSCC Code (licence plate) | Must be labelled | Must be labelled | 00 | n2 + n18 |
1) Transit Warehouse where the pallet is split/cross-docked, is stated in the VIA-field | ||||
2) Transport information is agreed between the parties | ||||
3) Example The Customers Ordering Number | ||||
4) Gross weight is the sum of weight of the products, packaging materials and pallet (load carrier) |
Example of shipping label for Customer packed unit
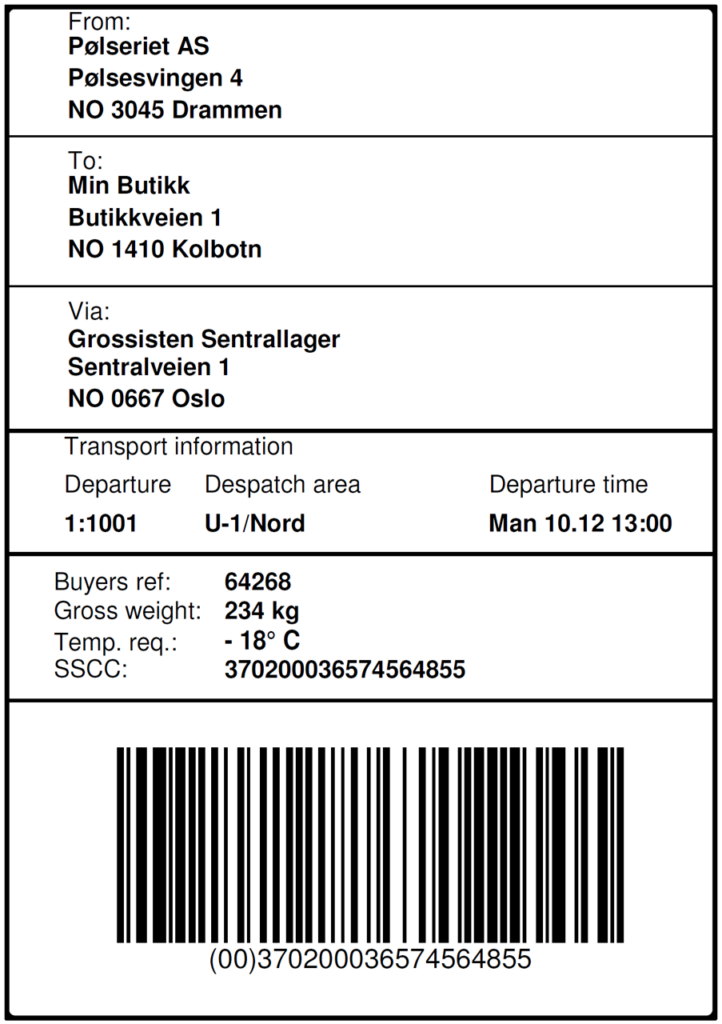
Guidelines for labels on Distribution Units (DU)
Placement of labels on pallet
Two types of labels shall be used; label for product information and label for transport information.
- The minimum requirement is that the pallet should be labelled on two sides with both label types; one of the short sides of the pallet and the right hand long side (seen from the short side).
- Product and transport label must be on the same side of the pallet.
- When multiple labels are used on the same side of the pallet, the labels should be placed underneath each other. The label that contains SSCC placed at the bottom.
- The labels should be placed so that the bottom of the lowest bar code should be at least 400 mm above the floor, and the top of the uppermost bar code should not be more than 800 mm above the floor.
- The label should be placed at least 50 mm from the vertical edge.
- For pallets lower than 400 mm the labels should be placed as high as possible.
- If all information is known at the time the pallet is labelled and there is space on the label, all information can be labelled on one single label.
- To ensure automatic reading of the bar codes Promotional Units, Customer packed pallet and Mixed pallet should only the transport label on the transport unit be readable
- Product label on Standard pallet with height 60 cm (Standard pallet – Low) should be placed as high as possible.
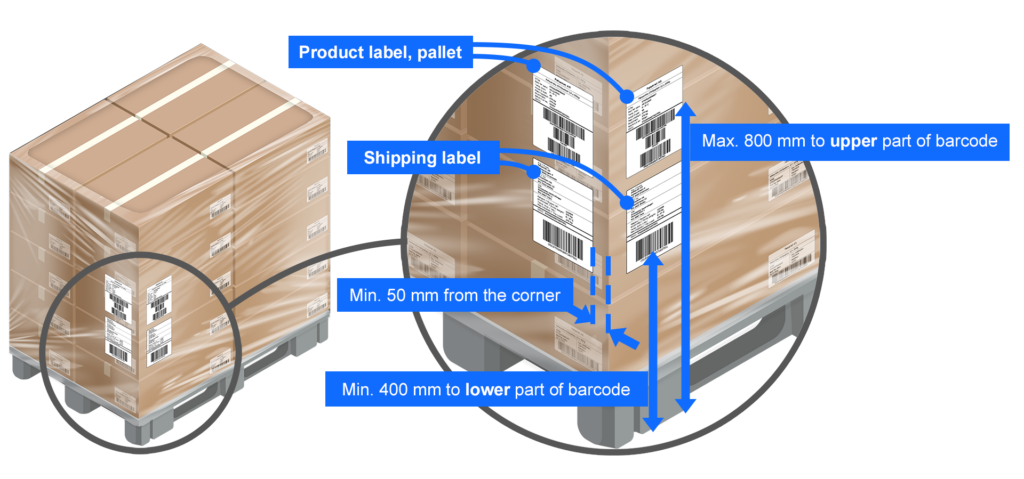
Identical information
Same information (GS1-128 AI) shall only appear once on the product and transport label.
This means in practice that the same information can not be repeated on the same label or that the same information may appear on multiple labels on the device (pallet).
The exception is SSCC which is allowed on both labels if it is an identical number used.
Size and design of the labels
The following recommendation applies:
- The width of the label should be 105 mm or 148 mm
- The height of the label may vary
Recommended formats are:
- A5 (148mm x 210mm)
- A6 (105mm x 148mm)
- 105 mm x 192 mm
Quality of labels
- It is a prerequisite that the labels are readable throughout the value chain for the entire life span of the unit
- It is a requirement that the quality of GS1-128 bar codes minimum meets print quality with “Grade C” according to Standard ISO / IEC 15416.
To achieve “Grade C” when reading, “Grade B” or better by printing is recommended - When affixing the labels, it is important to ensure that the bars in the GS1-128 symbol are correct and unbroken (avoid “wrinkling” on the label).
Valid pallets
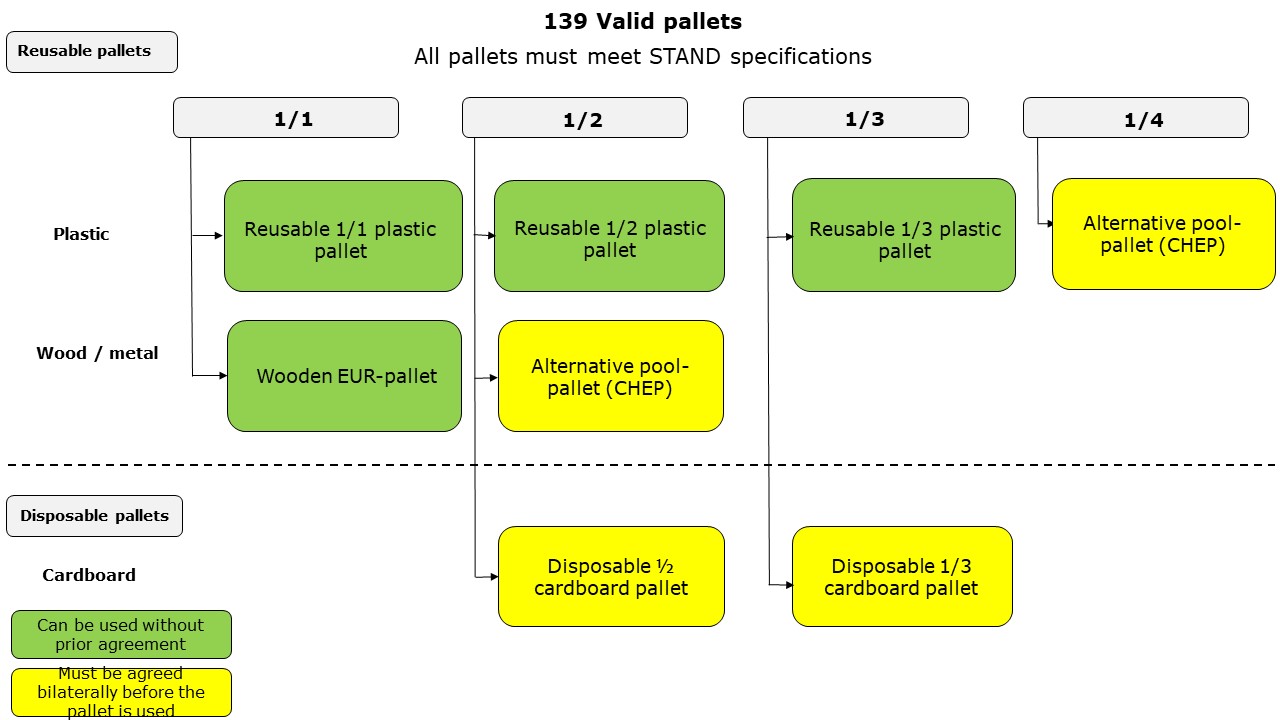
This is an animation that show what pallets are valid for distribution.
Requirements specifications can be downloaded here:
Requirements for approved EUR-pallets
Specification for reusable 1/1 plastic pallet
Specification for reusable 1/2 plastic pallet
Requirements specification for reusable 1/3 plastic pallet (from NLP)
Specification for reusable 1/4 plastic pallet
Requirements Specification reusable 1/2 wooden pallet
Requirements specification for 1/3 and 1/2 disposable cardboard pallet
Requirements for the design of the Distribution Unit (DU) and palletization
The Distribution Unit (DU) is the unit the Stock Keeping Units (SKU) is stacked on / packed in for transport to distributor.
Design of a Standard pallet (Standard pallet and Standard pallet – Low)
A Standard pallet must contain the same product (same GTIN) with a fixed number of Stock Keeping Units (SKU), in a fixed pallet pattern, with equal number of Stock Keeping Units (SKU)on each layer, and where labelling of unique product information on the Distribution Unit (DU) is possible.
The pallet structure shall contain as little excess volume of “air” as possible.
Standard pallet
Maximum pallet height must be 1200 mm incl. pallet. All pallets with total height above standard 1200mm with maximum height of 1250 mm to be agreed bilaterally between supplier and their customers.
Tolerance limit for existing products is 1249 mm.
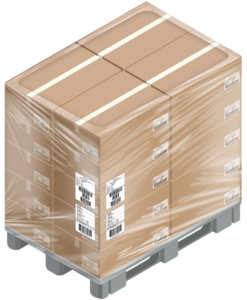
Standard pallet – Low
Maximum pallet height shall be 600 mm incl. pallet.
Standard pallet – Low is used for low-frequency products and for products with short shelf life.
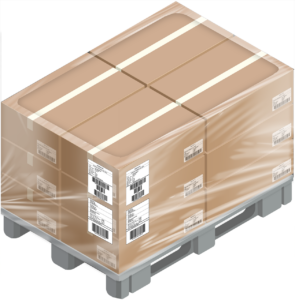
Principles for the construction of a palletpattern, central in calculation of top load weight, ref Top load labelling system.
When creating a pallet pattern, the following applies:
- A packaged Distribution Unit (DU) must be form stable and handling-friendly
- A Distribution Unit (DU) shall withstand regular transport, handling and storage through the value chain
- For single article Distribution Units (DU), all layers must contain the same number of Stock Keeping Units (SKU), and in a fixed pallet pattern
- Requirements for equal number of Stock Keeping Units (SKU) on each pallet / identical layer from pallet to pallet, with the possibility of variation between the layers
- The pallet should not have overhang
- The Stock Keeping Unit (SKU) should be placed on the pallet as it is exposed in the store
- Do not glue between pallet layers or between Stock Keeping Units (SKU) in the same pallet layer
- If a transport label or product label is attached directly to Stock Keeping Unit (SKU), the label must not overlap between 2 Stock Keeping Units (SKUs), either horizontally or vertically
- All pallets with total height above standard 1200mm with maximum height of 1250 mm to be agreed bilaterally between supplier and their customers.
Types of pallet pattern
When constructing Distribution Units (DU), the Stock Keeping Unit (SKU) must be placed in accordance with a given pallet pattern. These are referred to as bond stacking and column stacking. Pallets can also be built as a combination of bond stacking and column stacking.
Bond Stacking
Bond Stacking means that the units on every other layer are different, thus locking each other to a greater or lesser extent, but it reduces the compressive strength by approx. 40%.
Example of good pallet utilization and stacking with bond stacking, for good stability.
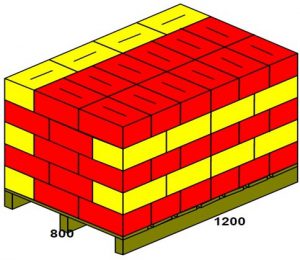
Column Stacking
Column stacking means stacking packages on top of each other without overlapping with other packages. This form of stacking gives maximum strength in terms of pressure load due to that the corners have better roll stiffness than the sides, but the stack gives poor stability without additional use of shrink wrap, strap, ribbon or similar.
Example of column stacking in the lower pallet layers, and bond stacking on the top layer. Combining the different stacking methods achieves good stack strength on the lower layers while the pallet is locked on top.
This is often a good alternative to intermediate pallet sheets.
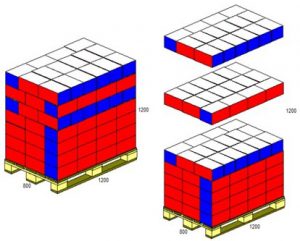
Use of plastic to secure the pallet through the value chain
- Shrink / stretch film must not be so tight that the packages are deformed
- Shrink / stretch film must be tight around to the pallet
- No tail of plastic must hang loose
- Shrink / stretch film must not cover the fork lift openings on the pallet
- Shrink / stretch film must not be fastened around the pallet blocks
Use of intermediate pallet sheets
Intermediate pallet sheets must be minimized and used only if this is necessary to ensure quality and transportability of the pallet.
Intermediate pallet sheets are preferred if the alternative to this is intermediate cartons, “Ears” on the Stock Keeping Unit (SKU) or use of corner trims.
Where intermediate pallet sheets are used, the following requirements apply:
- The pallet sheet to be used for standard euro pallet should have dimensions of 750 mm * 1150 mm, ie 50 mm less than the length and width of the current load carrier
- The pallet sheet must be of rigid cardboard or corrugated cardboard.
- The stiffness of the pallet sheet must pass the following test: If the short edge of the plate hangs 500 mm from a flat surface (eg a table), the pallet sheet must not bend down more than 50 mm, see illustration below
- No more than one intermediate pallet sheet between each layer
- The intermediate pallet sheet must not be fastened and be flat
- Only a whole intermediate pallet sheet, i.e. without holes or perforations, shall be used
- In case of questions, one is encouraged to contact the packaging supplier
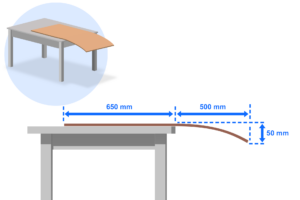
See also Automated storage at distributor – greater understanding of the depalletization process
Example of intermediate pallet sheet that does not meet quality requirements. The intermediate pallet sheet is a thin paper and is not suitable for automatic warehouse systems
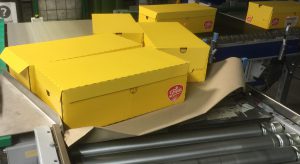
Example of what happens when using “thin paper” intermediate pallet sheets.
The sheet is hanging down in the robot. It blocks for sensors that check that the layer is separated from the rest of the pallet. The robot will stop, and manual error correction must be carried out before the machine can be restarted.
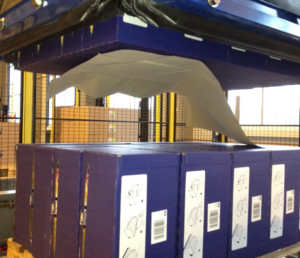
Example of pallet with intermediate pallet sheets, too big – hanging on outside the pallet.
Is not suitable.
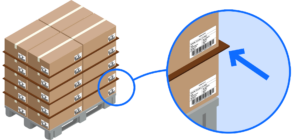
Intermediate pallet sheets with holes. Is not suitable.
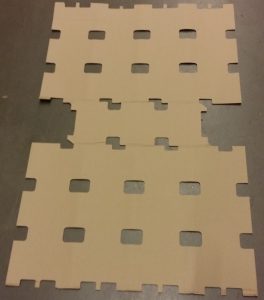
Endringslogg
Placement of Stock Keeping Unit (SKU) on pallet
It is a prerequisite for maintaining strength, that Stock Keeping Units (SKU) are placed within the edges of the pallet with a small margin.
Devices placed on or outside the edge can cause damage with subsequent reduced carrying capacity / risk of injury.
The pallet area should be utilized as best as possible with products. By following the Modular system optimal use of the pallet is ensured and reduces the risk of the load shifting during transport.
Overhang is not accepted.