Producing
This sub process describes the requirements, recommendations and guidelines STAND has, which may be relevant in production of a product to be traded in the grocery industry.
The process includes producing the product (Consumer Unit), packing it to a sales unit, usually a Stock Keeping Unit (SKU), fully packaged and labelled.
The areas described are:
- Total shelf life of the product
- Possible use of dynamic shelf life
- Traceability requirements for raw materials, input factors and finished products
- Labelling of traceability information on Consumer Unit (CU) and Stock Keeping Unit (SKU)
- 2D-labelling on Consumer Unit (CU)
- Labels on Stock Keeping Units (SKU)
- Content, and which information that should be in the bar code on the label
- Placement
- Requirements when using GS1-128
Guidelines and routines for tracking, recall and withdrawal
In its framework, STAND has defined guidelines, recommendations and best practices for how products should be marketed in the distribution chain, and how information on this should be exchanged between the parties.
Central to this is the consideration of the consumer and his expectation for safe food.
The guidelines for tracking, recall and withdrawal do not define food quality requirements, but describe what procedures and processes the industry has established to mitigate any unwanted effects should an incident or crisis occur in a product.
Best practices
The guidelines describe best practices in this area.
By following STAND’s framework, the guidelines will be achievable for all parties involved.
Some important prerequisites for best practice.
- Routines and processes must be simple, predictable and intuitive
- Products and deliveries / load carriers must be labeled in a unified, standardized and correct way so that they can be traced through the value chain.
- Product information must be registered in the Tradesolution EPD
- Detailed tracking information must be exchanged digitally between the parties and follow the products through the value chain.
- Action must be taken quickly when an incident or crisis occurs
By ensuring that a total industry complies with STAND’s framework, consumers’ demands and expectations for safe food are fully met.
Objective of the guidelines
The guidelines are aimed at “Contribute to meet consumers’ expectations for safe products”.
Target Audience:
- Anyone who may or will be involved in any recall or withdrawal
- Everyone involved in the production or labeling of products and packaging covered by the guidelines
Products / areas to which the guidelines apply:
- Recommended for food and non-food products, except pharmaceuticals
- Other inputs, plants, animals or foodstuffs
- Materials and articles that are intended to come into contact with, or may affect, inputs or foodstuffs.
Medicines are exempt from the guidelines. Here we refer to separate regulations, not described here.
Certain types of food may be subject to additional regulatory requirements beyond what is described here. An example is the EU’s new tobacco directive (EU 2014/40) which make the requirements for traceability of tobacco products more stringent, but is not described here.
Requirements for tracking information and labeling
The main purpose of the tracking information is to lay the groundwork for effective blocking, withdrawal or recall of products.
Central tracking information is:
- GTIN (Global Trade Item Number) – Unique identification of products
- GLN (Global Location Number) – Unique identification of trading parties, pick-up points, delivery points etc.
- SSCC (Serial Shipping Container Code) – Unique identification of load carriers / pallets
- Batch / lot number – A unique batch or lot number defined by supplier / manufacturer
- Shelf life – Either Best Before date or Last Consumption Date
It is a requirement that the products are labeled to enable tracking.
The marking must be affixed to the product packaging and legible.
The following applies to finished goods traded between supplier and distributor / retailer:
Information to be marked:
- The name of the supplier
- Product name/description
- Product number identified with a GTIN.
- Best before date / last day of consumption date, if required
- Batch / Lot number, if required
Load carrier (for example pallet) shall be marked with SSCC.
The sender must in his system have an overview of which recipient the product was sent to, and also the recipient must have an overview of which sender the product was received from. Both sender and recipient must be identified with GLN.
Sender shall in his system register:
- Quantity sent
- Shipping Date
- Reception date (if known)
Recipient shall in his system register:
- Quantity received
- Shipping date (if known)
- Reception Date
The following applies to raw materials and other inputs:
- GTIN should be used for identification of inputs / raw material, if available
- GLN should be used for identification of sender / suppliers, if available
More about tracking information and how the product can be tracked in the value chain is described here Recommended traceability methods in the value chain.
Guideline for labelling 2D barcodes on Consumer Units
Background
The need for information both in trade and to the consumer is constantly increasing. Today’s solution using the EAN-13 barcode does not provide opportunities for additional machine-readable information. The need for more information has led to products that have more than one bar code applied to Consumer Units, which creates challenges both at the checkout point (POS) and in the value chain. Often this is a QR code with a link to a website where the consumer can find more information.
In parallel with the need for more communication with consumers, a need is emerging at the retail level to gain more control over the traceability and expiry date of the products, to ensure safe food and reduce food waste. This is happening in most countries in the world. In Norway, GS1 Norway, together with Matvett, established a working group consisting of representatives from brand suppliers, grocery chains, system suppliers and other stakeholders to discuss these issues. These guidelines are a result of this work and have now been included as part of STAND’s framework for the Norwegian grocery industry.
Purpose of the use of 2D barcodes in Norwegian grocery
Although 2D barcodes are not the only solution to the challenges, this is the data carrier of the future, where the need for information is greater than just identifying a product with GTIN. 2D barcodes take up less space, can contain more information about the product, are a tool for reducing food waste and increase food security, are more flexible, and can be read by mobile phones. This provides an opportunity for increased consumer contact. In addition, 2D barcodes can solve all needs for information exchange throughout the supply chain, including being able to link to websites.
Different types of 2D barcodes
There are many different 2D barcodes, but only some of them can be used in connection with the GS1 standards, which are the standards used by the Norwegian grocery industry. The different 2D barcodes are also used for different purposes. This is regulated in GS1’s regulations, General Specifications. The difference between the different 2D barcodes helps to determine what they can be used for.
QR Code
The QR Code barcode is in the GS1 system defined to be used only with GS1 Digital Link URI syntax. In practice, this means that this should only be used for communication with the consumer via a URL that links to a website with more information that the consumer can read with his mobile phone. QR Code has grown to become the preferred barcode for consumer communication and most mobile phones today are able to read this with the built-in camera app in the phone. This means that the threshold for reading QR Code is low among consumers, and it is less need for training and communication to put functionality related to QR Code into production. Here you can find more information about QR codes.

GS1 Datamatrix
GS1 Datamatrix is a variant of Datamatrix that uses GS1 Element String syntax. This is the use of AI (Application Identifier) structure. This is a way of structuring the information in the barcode so that everyone who reads the barcode understands the content in the same way regardless of the order in which the information is printed and how much information is in the barcode. According to GS1 General Specifications, GS1 Datamatrix is only permitted for use on Consumer units with variable measure and prescription medicines. However, it is permitted to use it in limited pilots, for test purposes and in closed value chains under controlled conditions. The advantage of GS1 Datamatrix is that it has high compression and error correction. It can be printed both square and rectangular so that it can fit where there is not enough height, but enough width to get the information needed without compromising on size and thus readability. However, the rectangular version has a limit on the amount of data that can be used. GS1 Datamatrix is the only permitted barcode on prescription drugs. Here you can find more information about GS1 Datamatrix.
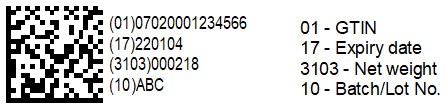
Content in barcode
A minimum requirement for information attributes has been defined for POS purposes.
This is:
- GTIN
- Best before date or Expiry date
- Batch/lot nr.
- Weight (for variable measure products).
It is possible to use other Application Identifiers for internal and/or external needs, but this is then up to each individual actor to use.
Allocation of total shelf life on a product
Reducing food waste is an overall goal in society. Food waste related to exceeding the limit values of shelf life between the parties in the value chain, constitutes a significant part.
Surveys shows that food waste are significantly reduced if the store and the consumer have a larger part of the total shelf life.
It is therefore a goal that the producer and distributor consume the least amount of available time and that the maximum amount of time is exposed to the consumer.
The grocery industry has defined one Table for allocation of shelf life of a product which regulates the responsibility for and expectations the recipient of products has, linked to shelf life. Online players with b2c sales will be defined as retailers when dividing total shelf life.
In case of minor exceedances of the table’s limit values, participants are expected to seek solutions that provide the lowest possible food waste.
The parties are encouraged to develop performance and collaborate to reduce consumption of shelf life.
Endringslogg
Determine total shelf life of a product and requirements for labelling this
The responsibility for determining type of shelf life labelling and total shelf life lies with the manufacturer. The shelf life is calculated from the time the product is ready for sales, for example from after the product has been matured and checked.
The actual shelf life of the product is affected by a variety of conditions, primarily the properties of the raw material and the external impact.
The manufacturers are encouraged to assess whether dynamic shelf life labelling can be practiced.
This means that total shelf life can be expanded when conditions allows for this to be done.
The number of days marked on a product may therefore be more than the number of shelf life on selected products.
According to the Mattilsynet (Norwegian Food Safety Authority), the use of dynamic shelf life is within the current regulations.
Labelling
The packaging (Consumer Units (CU) and Stock Keeping Units (SKU)) shall be labelled according to the manufacturer’s choice of type of shelf life and total shelf life.
Evaluate the use of dynamic shelf life
“Expiry date overdue” is the main reason for food waste in the value chain. A more flexible shelf life labelling throughout the year could help reduce food waste.
Shelf life is affected by several conditions that may vary. It is possible to specify increased shelf life in periods of time or for batches. This is termed as “dynamic shelf life». In practice, it means that overall shelf life can be expanded when conditions give the opportunity to do so.
The supplier should inform the customer if dynamic shelf life is applied.
According to the Mattilsynet (Norwegian Food Safety Authority), the use of dynamic shelf life within the current regulations: “It is the manufacturer who assesses and puts the shelf life of the food products. Manufacturers know the raw materials and processes used. Shelf life should be based on common and realistic conditions for transportation, storage and sales. This does not prevent manufacturers from taking into account that there may also be different external conditions for the shelf life of the foodstuffs. In practice, manufacturers often put the shelf life out of the most demanding but realistic conditions throughout the year. If the business has full control and overview of the terms, nothing stops them from choosing different shelf life throughout the year for the same product. This means the food is given a shelf life that is adapted to season, temperature and other conditions.”
More information can be found here: http://www.mattilsynet.no/mat_og_vann/merking_av_mat/generelle_krav_til_merking_av_mat/holdbarhetsmerking_paa_matvarer.2711
Examples of using dynamic shelf life that could have longer shelf life than often is the practice today:
- Different temperatures throughout the year
In order to make a realistic assessment, the producer assumes that the products are stored in normal outdoor / room temperature for a shorter period of time through the value chain, such as transshipment, stock refills in stores, consumer carts, transport from store to home and in the home (in and out of the fridge and on the kitchen table). In summer, the outdoor / room temperature is higher and thus has a greater impact on shelf life. To make a realistic assessment, it’s normal to take into account the assumptions in the summer period and determine the shelf life based on this, and the same shelf life is normally used throughout the year.
- Different shelf life based on different technology
Different companies may have different production methods and / or hygiene standards. To make a realistic assessment, the starting point is the technology that provides the shortest shelf life.
- Different shelf life of raw materials
The regulations or internal rules stipulate that raw materials that are up to x days “old” may be used at any given time in the manufacturing process. Then the shelf life is determined by using x-day-old raw material each time. This even though you often use fresher raw materials than x days.
- Different raw material quality
Raw material quality may vary naturally over a year, and in some cases this may affect shelf life. To make a realistic assessment, the raw material with the shortest shelf life is used, and normally uses the same shelf life of the finished foods throughout the year.
Dynamic shelf life and the EPD database
There is no need for any changes to the EPD database to utilize dynamic shelf life.
It is the product’s shortest shelf life during the year the supplier must register in the EPD database.
Purpose of labelling of Stock Keeping Unit (SKU) and Distribution Unit (DU)
The purpose of a standard for labelling of Stock Keeping Unit (SKU) and Distribution Unit (DU) with subsequent electronic data interchange (EDI) is to:
- Achieve an efficient flow of products from manufacturer to consumer
- Ensure traceability through the value chain, which is important in case an event or crisis occurs which requires a recall or withdrawal of the product
The basis for this is the labelling of each Distribution Unit (DU) with a unique SSCC.
This code is the main key in the electronic Despatch Advice and is linked to information about which GTIN which the Distribution Unit (DU) consists of, the number of Stock Keeping Units (SKU) batch / lot number and shelf life information if applicable.
SSCC is the most important key for traceability of Distributions Units (DU), see Recommended way to track and trace a product in the value chain.
For that reason SSCC shall not be reused until after a minimum of 6 years.
Recommended way to track and trace a product in the value chain
Efficiency and traceability are achieved primarily through:
- Synchronization of product information between the various parts in the value chain.
The purpose is for all players to obtain correct and coherent product information about the products. Between suppliers and retail chains in the Norwegian groceries sector the EPD database is used for the registration, quality assurance and distribution of product information.
- Electronic Data Interchange (EDI) between the actors.
The purpose is to reduce manual operations and reduce lead time in the value chain. The most widely used EDI messages are order, order confirmation, Despatch Advice and invoice.
- Standardized labelling of outer packaging.
The purpose is to contribute to faster and more efficient shipping, distribution and receipt of the products. A common labelling concept for the grocery industry is used here; GS1-128.
To ensure rational product and information flow in the distribution chain, STAND recommends a uniform labelling of Stock Keeping Units (SKU) and Distribution Units (DU).
This simplifies the labelling of the manufacturer / supplier, shipment by shipper / freight forwarders and merchandise at distributor / store.
This labelling concept also applies to types of transport units other than pallets.
For fish and fish products, the following applies:
STAND has decided to refer to Norwegian Standard NS17099:2020 “Information technology — Fishery and aquaculture products — Requirements for labelling of distribution units and pallets in the trade of fishery and aquaculture products” for products that fall under this category. This standard replaces todays NS9405: 2014 “Fish and fish products. Requirements for labelling of distribution units and pallets in the trade of fish and fish products», and is valid as from 30. September 2020.
It can be ordered from Standard Norway.
Product information on Stock Keeping Unit (SKU), with example of Stock Keeping Unit (SKU) label
Only product information should be labelled on a Stock Keeping Unit (SKU).
What information to be labelled depends on the type of product.
Intermediate Cartons shall be labelled as Stock Keeping Units (SKU)
Possible product information which SHALL or CAN be labelled on a Stock Keeping Unit (SKU)
GTIN – Global Trade Item Number
Includes GTIN-8 (8 digits), GTIN-12 (12 digits), GTIN-13 (13 digits) and GTIN-14 (14 digits).
All Stock Keeping Units (SKU) must have their own GTIN.
– For variable measure Stock Keeping Units (SKU), GTIN-14 with a leading digit 9 should be used.
– For other products, GTIN-13 is recommended.
Name of brand owner
– shall be shown in plain text either on the label or on the packaging.
Product name
– Must be written in plain text on the Stock Keeping Unit (SKU) product label.
– Must be based on the text in the Norwegian grocery data pool – EPD database, and consists of product name, attributes, – and product description.
– The product description labelled on the Stock Keeping Unit (SKU) must be identical to the text in the Despatch Advice and Invoice.
-Product description should also contain a package description: for example, Coffee 12 x 500gr.
Batch / lot number
– A number generated by the manufacturer, used to achieve full traceability of product lot/batches in the value chain
– GS1-128 AI 10 must be used.
Shelf life information (“Best before” date, alternatively “Expiry date”)
– Must be labelled on all Stock Keeping Units which has shelf life printed on the Consumer Unit (CU)
GS1-128 AI 15 shall be used for «Best before date”
GS1-128 AI 17 shall be used for «Expiry date»
Net weight
– GS1-128 AI 3103 shall be used for variable measure Stock Keeping Units (SKU).
– Net weight means weight of product excluding packaging (the same weight that is being invoiced).
Supplier’s item number
– can be labelled in plain text.
Table showing what SHALL or CAN be labelled:
Overview of product information that shall or may be labelled on Stock Keeping Unit (SKU): | ||||
Information | Human readable text | GS1-128 (bar code) | AI | Format |
GTIN for Stock Keeping Unit (SKU) | Must be labelled | Must be labelled | 01 | n2 + n14 |
Name of brand owner | Must be labelled | Not labelled | ||
Product name | Must be labelled | Not labelled | ||
Batch / lot number | Must be labelled | Must be labelled | 10 | n2 + an..20 |
Shelf life | Must be labelled if shelf life is marekd on the Consumer Unit (CU) |
Must be labelled if shelf life is marekd on the Consumer Unit (CU) |
15, alternatively 17 |
n2 + n6
|
Net weight | Must be labelled for products with variable measures |
Must be labelled for products with variable measures |
310x | n4 + n6
|
Supplier’s item no. | Can be labelled | Not labelled | ||
Example of GS1 Product label for Stock Keeping Unit (SKU), for a product with “Best before” date and a fixed weight:
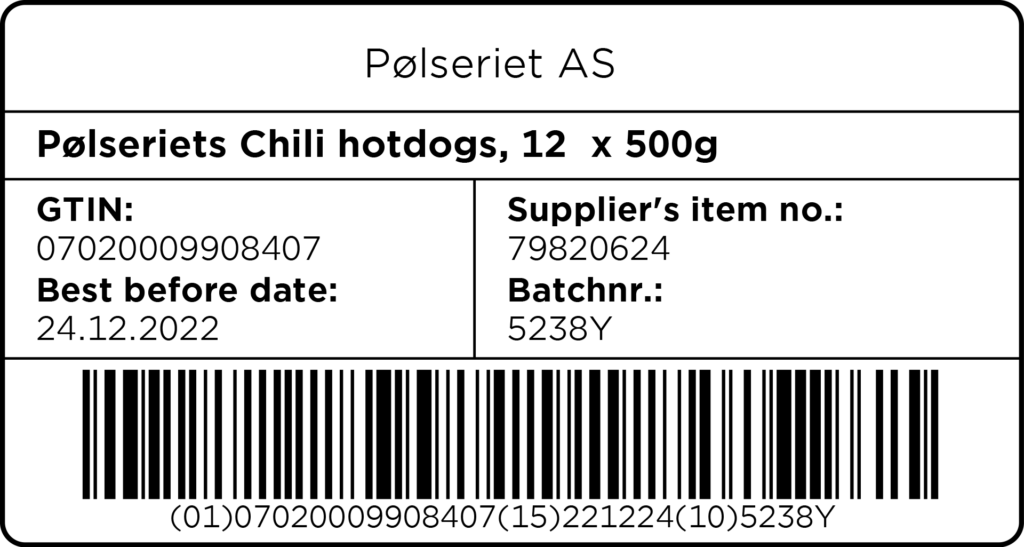
Example of GS1 Product label for Stock Keeping Unit (SKU), for a product with “Expiry date” and variable measures:
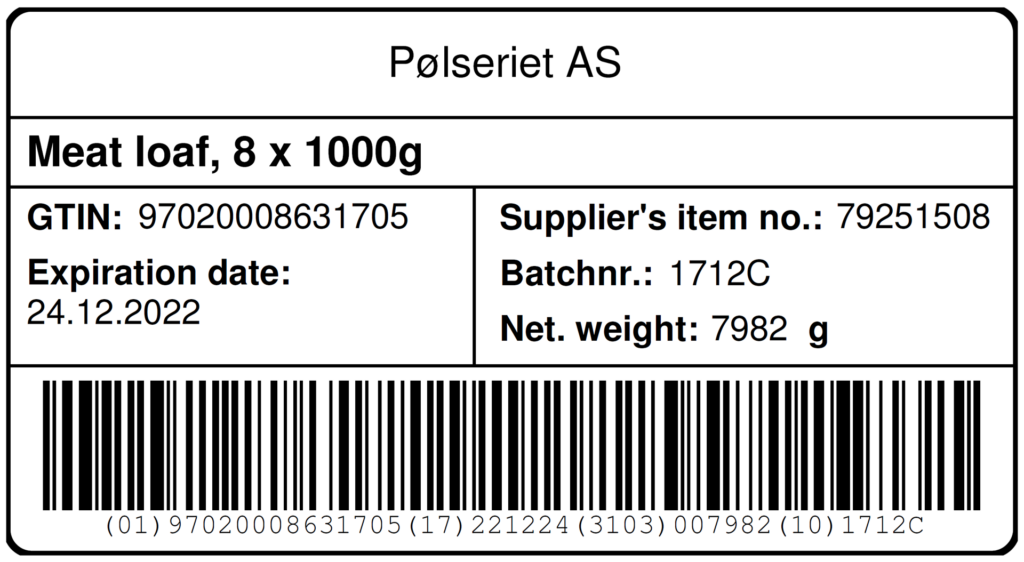
Guidelines for labelling of Stock Keeping Units (SKU)
Type of bar code symbol
When labelling with bar code on Stock Keeping Units (SKU) GS1-128 bar code shall be used.
Identical information
Same information (GS1-128 AI) should only occur once per label.
Size and design of labels
Since the shape and size of the Stock Keeping Units (SKU) is highly varied, size and design of the label may also vary.
Quality of labels
It is a prerequisite that the labels are readable throughout the value chain for the entire life span of the unit. Therefore, the quality of GS1-128 bar codes must minimum fulfill print quality with “Grade C” according to standard ISO / IEC 15416.
To achieve “Grade C” when reading, “Grade B” or better is recommended at printing.
Quality of labels and bar codes can be verified at GS1 Norway.
Placement of labels on Stock Keeping Units (SKU)
It is recommended that the Stock Keeping Units (SKU) is labelled on two sides.
If labelling can only be done on one side, the label on the Stock Keeping Unit (SKU) must be on the same side as one of labels on the pallet (consistent orientation).
By column stacking the Stock Keeping Unit (SKU) label will be oriented towards one pallet label (either on the short or long side of the pallet).
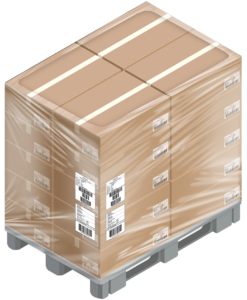
By bond stacking (like bricks) the Stock Keeping Unit (SKU) label could be oriented towards the two labels of the pallet. That is, both on the short and the long side of the pallet.
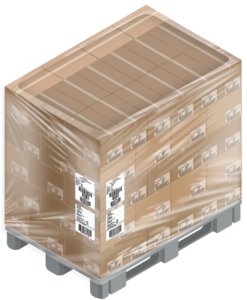
Bar codes
The following recommendations apply to GS1-128 bar code symbols:
- The orientation of the bar code should be such that the bars are vertical (picket fence).
- Size factor is in the range of 25 to 94% of nominal size.
- The minimum bar code height is 13 mm.
- Minimum 5 mm height on human readable text.
- The location of the bar code should be such that the bottom of the bar code is about 32 millimeters from the bottom of the Stock Keeping Unit (SKU).
- The bar code symbol included quiet zone (margins), must be at least 19 millimeters from a vertical edge to avoid damage to the label.
- If the height of the Stock Keeping Unit (SKU) is less than 50 mm, the bar code should be placed as high as possible and information to be written in plain text can be placed to the left of the bar code
Placement of bar code symbols on the Stock Keeping Unit (SKU)
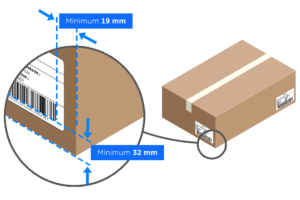
Placement of bar code symbols on Stock Keeping Units (SKU) with height less than 50 mm
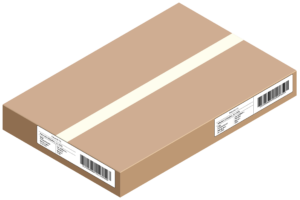
Bar code requirements for labelling with GS1-128 on Distribution Units (DU)
Bar code label with GS1-128 bar codes shall be done according to GS1 General Specifications Chapter 5.4.
Note in particular:
- Size factor is in the range of 50 to 94% of nominal size.
- The minimum bar code height is 32 mm.
- When labelling GTIN (AI 01 and AI 02) always use 14 digits.
When GTIN has 13 digits, you must enter a leading 0 (ex. 07038010000065). - For bar code labelling with GS1-128, a separator, called Function Code 1 (FNC1), is used between the individual information elements (AI’s).
This applies except for the AI’s that have predefined fixed length.
The following AI’s in this document have predefined length AI 00, AI 01, AI 02, AI 15. - It is recommended to have the AI’s to be followed by FNC1 at the end of the bar code, as the FNC1 code may be omitted.
- It is important to the requirements for quiet zone (margins) to be adhered to.
At size factor 50%, the right and left quiet zone margin is 5 mm, and at the size factor 94% the quiet zone margins are 9.4 mm.