Time-managed or inventory-managed assortment change
Assortment change can be done inventory-managed or time-managed.
Inventory-managed assortment change means that outgoing products are sold until inventory is at a low level or sold out and then sales of the new product starts.
In the case of inventory-managed assortment change, new products will replace an outgoing item and / or take over its place in the shelf – link / product connection is used. Sales start will depend on inventory and sales on outgoing item. The supplier and the retail chain must agree which stocks are included and calculate the date of the transition. Campaigns or other steps to make the change can be agreed. It is normal to set a final deadline for the delivery of the outgoing item.
Inventory-managed assortment change significantly reduces the risk of empty shelves and losses throughout the value chain and should be chosen if possible.
Optimal inventory-managed assortment change requires close collaboration between supplier and individual wholesaler, including dialogue on inventories and sales development. It will not be pre-orders from wholesaler in U-3 if inventory-managed in-phase is used. Order and startup are bilaterally agreed.
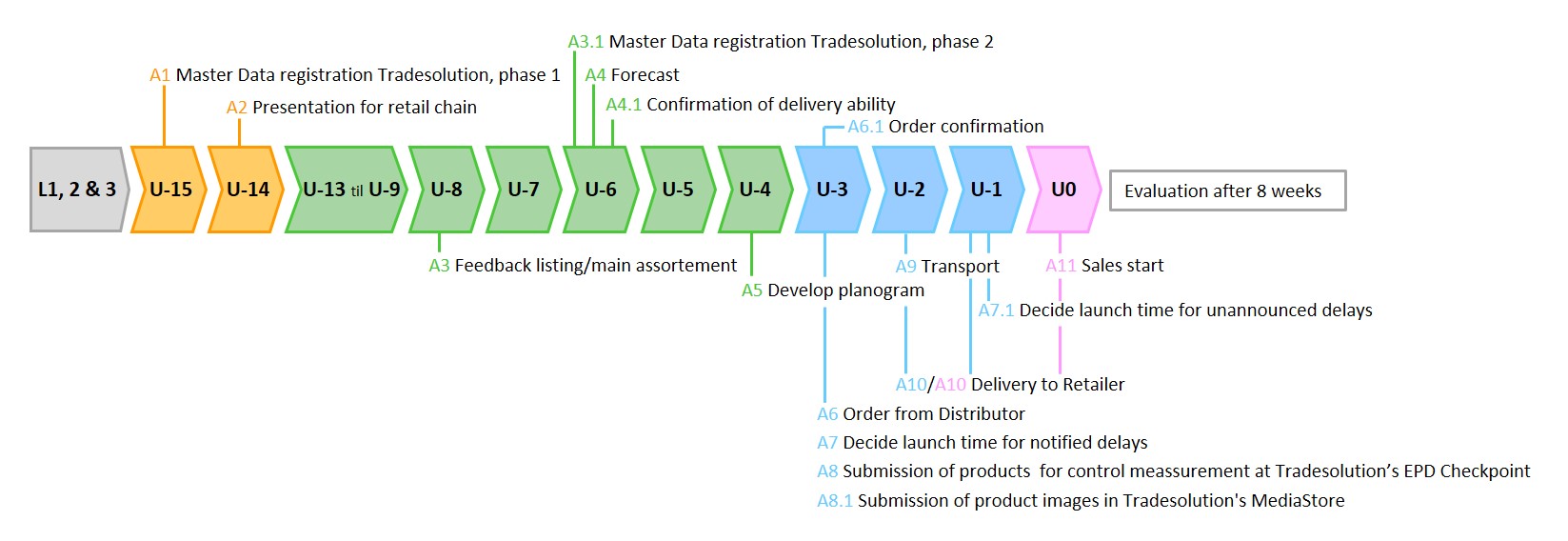
Time-managed assortment change implies that a date for the start of sale of products is set. Time-managed assortment change is selected when inventory-managed is not optimal, eg by phasing in products that receive heavy sales support or where the physical attributes of the product require rebuilding of shelves. With time-managed in-phase, relevant wholesale warehouses and stores must be filled up at the same time. The volume for this is significant and must be calculated separately – referred to as «pipeline fill»
News to be distributed in several trading chains is launched in one of the industry’s joint launch time frames.